Novel oil-saving spindle with dynamic self-rotating airflow gap sealing
A technology of airflow gap and rotating airflow, which is applied in the direction of textiles and papermaking, can solve the problems of unsatisfactory fuel saving effect and inability to implement effective sealing effect, and achieve the effect of enhancing dynamic sealing effect and avoiding oil mist leakage
- Summary
- Abstract
- Description
- Claims
- Application Information
AI Technical Summary
Problems solved by technology
Method used
Image
Examples
Embodiment Construction
[0035] The technical solutions in the embodiments of the present invention will be further described below in conjunction with the drawings in the embodiments of the present invention.
[0036] Figure 1 It is a structural diagram of a separate spindle in the prior art, consisting of a spindle bar 1-1, a spindle disc 1-2, a bearing washer 1-3, an upper bearing 1-4, an upper bearing seat 1-5, a nylon ring 1-6, a spindle It consists of feet 1-7, center sleeve 1-8, vibration-absorbing coil spring 1-9, ingot bottom 1-10, and ingot hook joint 1-11.
[0037] Figure II It is a structural diagram of an elastic tubular pointed spindle in the prior art, consisting of a spindle rod 2-1, a spindle disc 2-2, a bearing washer 2-3, an upper bearing 2-4, an upper bearing seat 2-5, and a spindle foot 2- 7. It consists of elastic tube 2-8, shock-absorbing coil spring 2-9, ingot bottom 2-10, and ingot hook joint 2-11.
[0038] Figure three It is a structural diagram of an elastic tubular f...
PUM
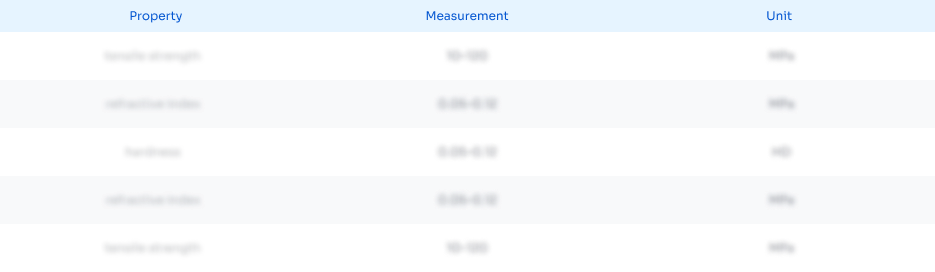
Abstract
Description
Claims
Application Information

- R&D
- Intellectual Property
- Life Sciences
- Materials
- Tech Scout
- Unparalleled Data Quality
- Higher Quality Content
- 60% Fewer Hallucinations
Browse by: Latest US Patents, China's latest patents, Technical Efficacy Thesaurus, Application Domain, Technology Topic, Popular Technical Reports.
© 2025 PatSnap. All rights reserved.Legal|Privacy policy|Modern Slavery Act Transparency Statement|Sitemap|About US| Contact US: help@patsnap.com