Step-by-step calibration method for camera parameters of binocular stereoscopic vision system
A technology for binocular stereo vision and camera parameters, which is applied in image analysis, image data processing, instruments, etc., and can solve the problems of complex calibration methods and poor real-time performance.
- Summary
- Abstract
- Description
- Claims
- Application Information
AI Technical Summary
Problems solved by technology
Method used
Image
Examples
Embodiment Construction
[0038] The implementation of the present invention will be described in detail below in conjunction with the accompanying drawings and technical solutions.
[0039] figure 1 It is a schematic diagram of the device structure of the present invention. The model of the binocular vision camera adopted in this embodiment is: SVCam-svs11002, and the resolution is 4008×2672; the high-precision electronic control platform adopts Physik Instrumente (PI), and the displacement accuracy reaches 0.1 μm ; The length of the high precision standard ruler is 2001.464mm. Calibration is carried out at the experimental site with a measurement range of 3m×2.5m, and the distance from the checkerboard calibration board to the camera is about 5m.
[0040] In this method, the internal parameter matrix of the camera is calibrated off-line in the laboratory first, and the camera is driven by a high-precision electronic control platform to perform two independent three-orthogonal movements. Parameters;...
PUM
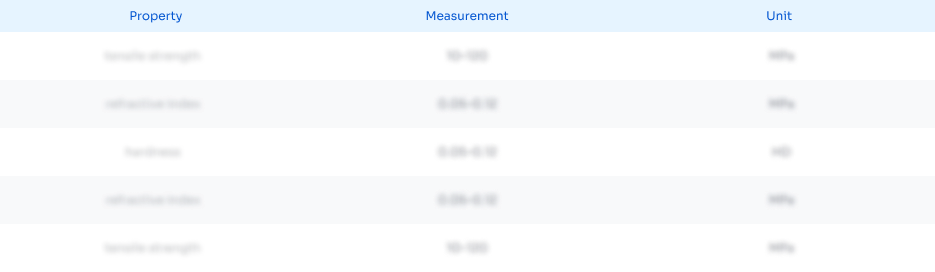
Abstract
Description
Claims
Application Information

- R&D
- Intellectual Property
- Life Sciences
- Materials
- Tech Scout
- Unparalleled Data Quality
- Higher Quality Content
- 60% Fewer Hallucinations
Browse by: Latest US Patents, China's latest patents, Technical Efficacy Thesaurus, Application Domain, Technology Topic, Popular Technical Reports.
© 2025 PatSnap. All rights reserved.Legal|Privacy policy|Modern Slavery Act Transparency Statement|Sitemap|About US| Contact US: help@patsnap.com