Method and device for calibrating sensor postures of robot in real time and terminal equipment
A sensor and robot technology, applied in the field of sensor control of industrial robots, can solve the problem of not being able to reflect the relationship between sensors and robots in real time
- Summary
- Abstract
- Description
- Claims
- Application Information
AI Technical Summary
Problems solved by technology
Method used
Image
Examples
Embodiment 1
[0072] Such as figure 1 As shown, the embodiment of the present invention provides a method for real-time calibration of the posture of a robot sensor. The robot is provided with a binding position of the sensor, and the binding position can be located at any position of the robot, such as a robot end effector. , A robot image collector, etc., which are not specifically limited in the embodiment of the present invention; the sensor can be set in the binding position, and the method for real-time calibration of the robot sensor posture includes:
[0073] S101. Establish a robot motion coordinate system and a sensor coordinate system.
[0074] In the above step S101, the normal robot has its own motion coordinate system to determine the position and posture of the robot; and the sensor, as a signal input device, controls the cap by pushing, pulling, pressing, lifting, rotating and tilting. , Can generate data describing the position and attitude such as translation, pitch, roll and ...
Embodiment 2
[0129] Such as Figure 4 As shown, the embodiment of the present invention provides an apparatus 40 for real-time calibration of the posture of a robot sensor. The robot is provided with a binding position of the sensor, the sensor is arranged at the binding position, and the real-time calibration robot The sensor attitude device 40 includes:
[0130] The coordinate system establishment module 41 is used to establish the robot motion coordinate system and the sensor coordinate system.
[0131] The first calculation module 42 is configured to control the directional movement of the sensor, obtain six-dimensional pose data, and calculate the initial posture relationship of the sensor coordinate system relative to the robot motion coordinate system.
[0132] The second calculation module 43 is configured to calculate the posture transformation amount of the binding position relative to the robot.
[0133] The third calculation module 44 is configured to calculate the sensor relative to t...
PUM
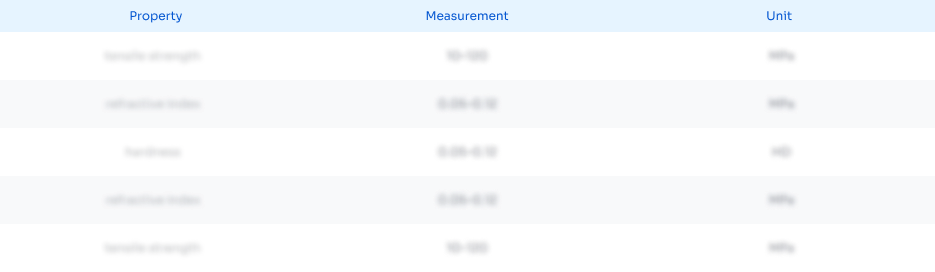
Abstract
Description
Claims
Application Information

- R&D
- Intellectual Property
- Life Sciences
- Materials
- Tech Scout
- Unparalleled Data Quality
- Higher Quality Content
- 60% Fewer Hallucinations
Browse by: Latest US Patents, China's latest patents, Technical Efficacy Thesaurus, Application Domain, Technology Topic, Popular Technical Reports.
© 2025 PatSnap. All rights reserved.Legal|Privacy policy|Modern Slavery Act Transparency Statement|Sitemap|About US| Contact US: help@patsnap.com