A Frequency Modulation Method for Large Structural Components Based on Bottom Load Allocation
A technology for large-scale structural parts and load distribution, which is applied in design optimization/simulation, special data processing applications, etc., and can solve problems such as poor implementability of equipment and large casings
- Summary
- Abstract
- Description
- Claims
- Application Information
AI Technical Summary
Problems solved by technology
Method used
Image
Examples
Embodiment Construction
[0028] The present invention will be further described below in conjunction with the accompanying drawings and embodiments.
[0029] The invention relates to the resonance problem induced by the natural frequency of a certain generator body structure being close to the working frequency. By adjusting the bottom load distribution of the generator, the natural frequency is effectively reduced and the resonance phenomenon is avoided. In the actual application process, the specific steps are as follows:
[0030] Step 1: Conduct modal tests on the generator structure to obtain frequency response curves (such as figure 2 ), calculate the natural frequency f of each order according to the frequency response curve.
[0031] Step 2: Compare the natural frequency f of the generator body structure with the operating frequency f 0 , to determine the resonance state and resonance order (the k-th order structural resonance frequency f k close to the operating frequency f 0 ), and use m...
PUM
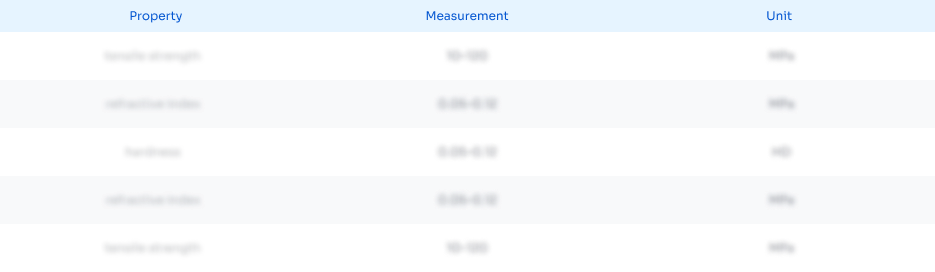
Abstract
Description
Claims
Application Information

- R&D
- Intellectual Property
- Life Sciences
- Materials
- Tech Scout
- Unparalleled Data Quality
- Higher Quality Content
- 60% Fewer Hallucinations
Browse by: Latest US Patents, China's latest patents, Technical Efficacy Thesaurus, Application Domain, Technology Topic, Popular Technical Reports.
© 2025 PatSnap. All rights reserved.Legal|Privacy policy|Modern Slavery Act Transparency Statement|Sitemap|About US| Contact US: help@patsnap.com