Quick analysis and design method for heat protection system of aerospace flying vehicle
An aerospace vehicle, rapid analysis technology, applied in computer-aided design, design optimization/simulation, instruments, etc., can solve the problem of inability to realize automatic thermal protection system scheme selection, and there is no mature tool software and method for the thermal protection system of the entire aircraft. And other issues
- Summary
- Abstract
- Description
- Claims
- Application Information
AI Technical Summary
Problems solved by technology
Method used
Image
Examples
Embodiment Construction
[0072] The present invention will be further described below in conjunction with accompanying drawings and examples. The one-dimensional unsteady heat transfer process of a typical 15° semi-cone obtuse pyramid structure is taken as an example. The structure is selected from the NASA report "Effects of Angle of Attack and Bluntness on Laminar HeatingRate Distributions of a 15°Cone at a MachNumber of 10.6", the structure size is as follows image 3 As shown, the tip of the structure is a ball cap with a radius of 0.0095m, and the rear part is a cone with a half-cone angle of 15° as a whole.
[0073] (1) Calculation of thickness at nodes
[0074] Select reinforced carbon-carbon composite (RCC) (material density 1580kg / m 3 , specific heat 0.77kJ / kg-K, thermal conductivity k, 4.3W / m-K, radiation coefficient, 0.79), the default wall temperature is 300K, and the allowable temperature of the material is 1900K (for the convenience of case application, the allowable temperature of the...
PUM
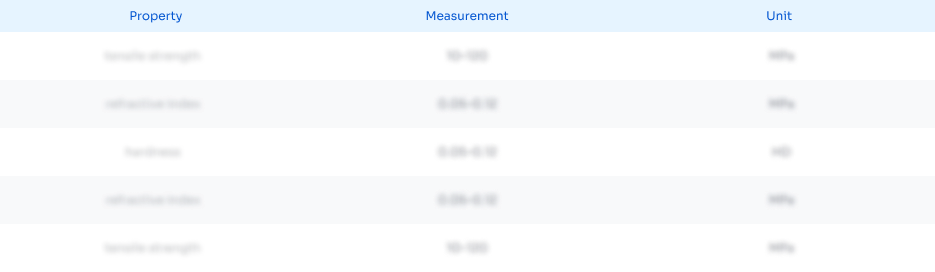
Abstract
Description
Claims
Application Information

- Generate Ideas
- Intellectual Property
- Life Sciences
- Materials
- Tech Scout
- Unparalleled Data Quality
- Higher Quality Content
- 60% Fewer Hallucinations
Browse by: Latest US Patents, China's latest patents, Technical Efficacy Thesaurus, Application Domain, Technology Topic, Popular Technical Reports.
© 2025 PatSnap. All rights reserved.Legal|Privacy policy|Modern Slavery Act Transparency Statement|Sitemap|About US| Contact US: help@patsnap.com