Large wide airliner multi-position maintenance hangar roof diagonal truss structural system
A truss structure and multi-camera technology, applied in roofs, building components, building structures, etc., can solve the problems of large internal force of gate truss members, difficulty in realization, poor collapse resistance of central columns, etc., and achieve simple cross-section selection , The effect of reducing the maximum internal force and reducing the burden
- Summary
- Abstract
- Description
- Claims
- Application Information
AI Technical Summary
Problems solved by technology
Method used
Image
Examples
Embodiment 1
[0060] Embodiment one sees Figure 6-10 As shown, the hangar is a single-span hangar. This large-scale wide-body passenger aircraft multi-stand maintenance hangar roof oblique truss structure system includes roof support columns arranged at intervals along the three sides of the hangar and fixed on the roof support columns. The roof steel structure at the top of the column; it also includes a gate truss support column arranged along the open side of the hangar and a gate truss 2 fixed on the top of the gate truss support column, and the roof steel structure is connected with the gate truss 2 .
[0061] The roof steel structure includes a main structural frame 3 covering the hangar, and also includes a diagonal truss 4 and a straight truss 5 arranged inside the main structural frame. It can be formed by truss members replacing the corresponding positions of the main structural members, and the straight truss 5 intersects with the oblique truss 4 . In this embodiment, the incli...
Embodiment 2
[0069] Embodiment two see Figure 11-16 As shown in , 18, the hangar is a two-span hangar, so different from Embodiment 1, the gate truss support column also includes the gate truss middle support column 8 set at the sub-span of the multi-span hangar. There is at least one oblique truss 4 at the sub-span. In this embodiment, there are two. One end of the two oblique trusses is connected as a whole and placed on the supporting column 8 of the gate truss. The other end of the two oblique trusses The parts are all supported and connected to the gable support column 7a behind the oblique truss. The angle between the oblique truss 4 and the gate truss 2 can be set to 30-60 degrees according to the stress situation, wherein 45 degrees is the optimal stress angle, which is 45 degrees in this embodiment. So far, the inclined trusses installed in each span of the hangar are arranged in two V-shaped, two mirror-symmetrical arrangements, and four in a W-shape.
[0070] Since the transm...
PUM
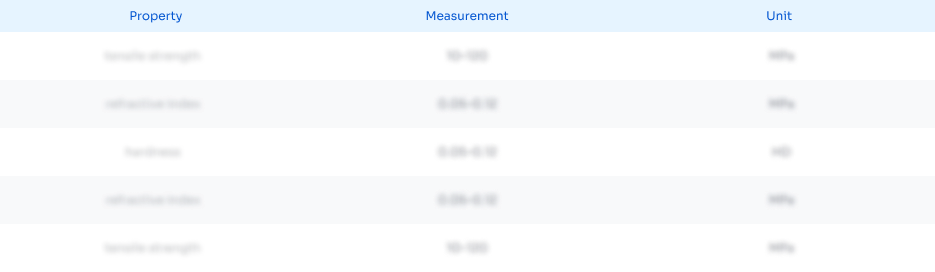
Abstract
Description
Claims
Application Information

- R&D
- Intellectual Property
- Life Sciences
- Materials
- Tech Scout
- Unparalleled Data Quality
- Higher Quality Content
- 60% Fewer Hallucinations
Browse by: Latest US Patents, China's latest patents, Technical Efficacy Thesaurus, Application Domain, Technology Topic, Popular Technical Reports.
© 2025 PatSnap. All rights reserved.Legal|Privacy policy|Modern Slavery Act Transparency Statement|Sitemap|About US| Contact US: help@patsnap.com