Control method for carbon content of FeV80 alloy
A control method and carbon content technology, applied in the field of metallurgy, can solve problems such as no public reports, and achieve the effect of easy operation
- Summary
- Abstract
- Description
- Claims
- Application Information
AI Technical Summary
Problems solved by technology
Method used
Examples
Embodiment 1
[0023] at 8t V 2 o 5 The raw materials are smelted in three phases and the slag is discharged twice. Smelting Raw Material V 2 o 5 , Fe, Al, and lime have carbon contents of 0.01%, 0.06%, 0.13%, and 0.33%, respectively. For conventional smelting, the total electrification time is 88 minutes. After the third phase of smelting, the TV content in the slag is 1.30%, the ferrovanadium smelting yield is 96.8%, and the alloy carbon content is 0.15%.
Embodiment 2
[0025] at 8t V 2 o 5 The raw materials are smelted in three phases and the slag is discharged twice. Smelting Raw Material V 2 o 5 , Fe, Al, and lime have carbon contents of 0.01%, 0.06%, 0.13%, and 0.33%, respectively. In the third stage, 480kg of decarburizer FeO was mixed into the batching, and the total electrification time was 95min (extra electrification for 7min before casting). After the smelting, the TV content in the slag is 1.32%, the smelting yield of ferrovanadium is 96.6%, and the carbon content of the alloy is 0.08%.
Embodiment 3
[0027] at 3t V 2 o 5 The raw material is smelted according to the one-step process. After the smelting is completed, the slag and iron are produced together, and the smelting raw material V 2 o 5 The carbon contents of Fe, Al, and lime are 0.01%, 0.06%, 0.15%, and 0.36%, respectively. Add 100kg of decarburizer FeO and spread it on the bottom of the casting ingot mold, and the total power-on time is 25min. After the smelting, the TV content in the slag is 1.36%, the smelting yield of ferrovanadium is 96.3%, and the carbon content of the alloy is 0.07%.
PUM
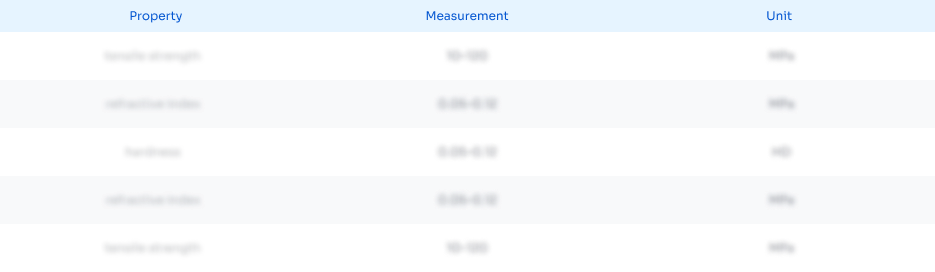
Abstract
Description
Claims
Application Information

- R&D Engineer
- R&D Manager
- IP Professional
- Industry Leading Data Capabilities
- Powerful AI technology
- Patent DNA Extraction
Browse by: Latest US Patents, China's latest patents, Technical Efficacy Thesaurus, Application Domain, Technology Topic, Popular Technical Reports.
© 2024 PatSnap. All rights reserved.Legal|Privacy policy|Modern Slavery Act Transparency Statement|Sitemap|About US| Contact US: help@patsnap.com