A method for measuring the three-dimensional spatial distribution of magnetically induced strain inside a material
A technology of magneto-induced strain and three-dimensional space, which is applied to the use of wave/particle radiation for material analysis, measurement devices, and analysis of materials. It can solve the problems of measurement environment influence, measurement direction limitation, etc., and solve the problem of single measurement direction limitation. Effect
- Summary
- Abstract
- Description
- Claims
- Application Information
AI Technical Summary
Problems solved by technology
Method used
Image
Examples
Embodiment 1
[0030] Such as image 3 As shown, the specific steps of the method for measuring the three-dimensional spatial distribution of magnetically induced strain inside the material of the present invention are as follows:
[0031] a. Geometric layout
[0032] Install and fix the goniometer 1 used for measuring the azimuth on the load-bearing platform 2 that has been emptied and reset, and the spinning disk 3 is installed on the rotating circle 8 and returns its rotation and rotation angle to zero. The neutron light source 9 and the detector 12 are respectively located on both sides of the goniometer 1, and the centers of the neutron light source 9 and the detector 12 are respectively at the angle bisector and the angle measuring line between the lines connecting the center of the rotating circle 8. Platform 1 is parallel to the vertical circular plane.
[0033] b. Sample installation
[0034] The sample rod 4 is fixed on the spin disk 3, and the sample 6 is installed and fixed in...
PUM
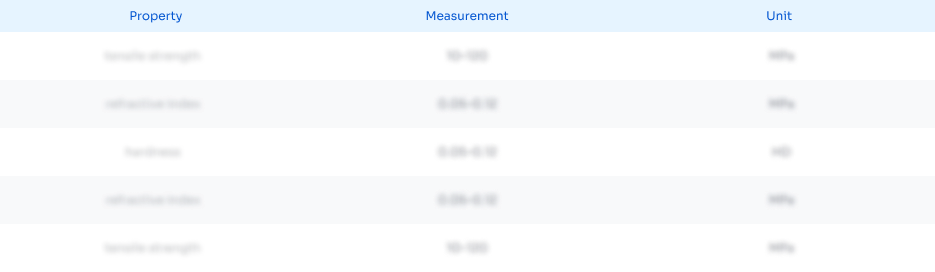
Abstract
Description
Claims
Application Information

- R&D Engineer
- R&D Manager
- IP Professional
- Industry Leading Data Capabilities
- Powerful AI technology
- Patent DNA Extraction
Browse by: Latest US Patents, China's latest patents, Technical Efficacy Thesaurus, Application Domain, Technology Topic, Popular Technical Reports.
© 2024 PatSnap. All rights reserved.Legal|Privacy policy|Modern Slavery Act Transparency Statement|Sitemap|About US| Contact US: help@patsnap.com