A deep shaft multi-rope winding hoist and winding method
A hoist and shaft technology, which is applied in the field of winding and hoisting of personnel and materials, can solve the problems of reducing hoisting efficiency, thick wire rope diameter, and increase of wire rope self-weight, etc., and achieves the effect of increasing quantity, increasing service life and reducing motor cost.
- Summary
- Abstract
- Description
- Claims
- Application Information
AI Technical Summary
Problems solved by technology
Method used
Image
Examples
Embodiment 1
[0035] Embodiment 1, as figure 1 with 2 As shown, the deep vertical shaft multi-rope winding hoist of the present invention is mainly composed of a sky wheel train and a drive system located above the wellhead, and the drive system controls the steel wire rope that bypasses the sky wheel and is connected to the lifting container. The sky wheel train includes The upper sky gear train 1 and the lower sky gear train 3; the described drive system includes: as Figure 7 Shown front drive motor group 5 and rear drive motor group 16, front axle group 7, rear axle group 11, as Figure 8 Shown front drum group 9 and rear drum group 10, front and rear drum group 9,10 are respectively installed on the front and rear axle group 7,11, and the left and right ends of front and rear axle group 7,11 are provided with successively respectively Brake disc 12 and driving motor; the two ends of the front shaft 7 of the front drum group 9 are respectively connected to the output shafts of the fro...
Embodiment 2
[0045] Embodiment 2, as image 3 , 4 As shown, it is basically the same as Example 1, and the same part is omitted. The difference is that the number of rollers in the front and rear roller groups is 1, specifically:
[0046] Engage between the front gear one 8-1 and the rear gear one 17-1 on the left and right sides of the hoist. When the front lifting wire rope 2 was promoted, the driving motor 15 on the rear side rotated clockwise; the driving motor 5 rotating direction on the front side was opposite to the rear side motor 14 rotating direction, which was counterclockwise. When the rear hoisting wire rope 4 was promoted, the front drive motor unit 5 rotated clockwise; the rear side motor 14 rotation direction was opposite to the front drive motor unit 5 rotation direction, which was counterclockwise.
Embodiment 3
[0047] Embodiment 3, as Figure 5 , 6 As shown, it is basically the same as Example 1, and the same part is omitted. The difference is that the number of rollers in the front and rear roller groups is 3, specifically:
[0048] The front gear 1 8-1 on the front side of the drum in the front drum group 9 meshes with the front gear 2 8-2 through a front auxiliary wheel 15-1, and the front gear 2 8-2 and the front gear 3 8-3 Engage with 1 auxiliary wheel 15-2, the rear gear one 17-1 and the rear gear two 17-2 on the left and right sides of the drum in the rear drum group 10 are engaged by the rear auxiliary wheel 14-1, and the rear gear two 17-2 2 meshes with the gear 17-3 through an auxiliary wheel 14-2. The rotation directions of the front and rear drive motor groups 5 and 16 are opposite, that is, when the front hoisting wire rope 2 is lifted, the rear drive motor group 16 rotates clockwise; on the contrary. When the rear wire rope 4 was promoted, the drive motor 5 on the ...
PUM
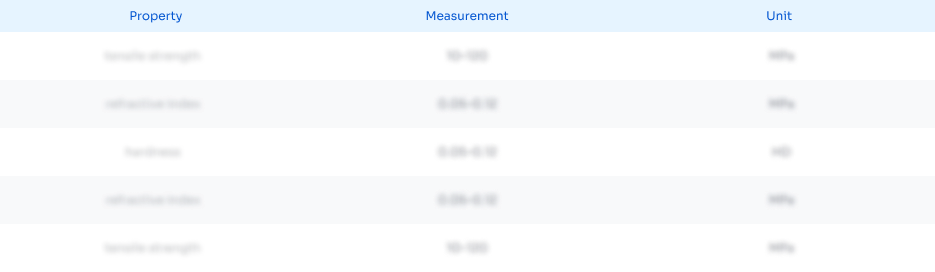
Abstract
Description
Claims
Application Information

- Generate Ideas
- Intellectual Property
- Life Sciences
- Materials
- Tech Scout
- Unparalleled Data Quality
- Higher Quality Content
- 60% Fewer Hallucinations
Browse by: Latest US Patents, China's latest patents, Technical Efficacy Thesaurus, Application Domain, Technology Topic, Popular Technical Reports.
© 2025 PatSnap. All rights reserved.Legal|Privacy policy|Modern Slavery Act Transparency Statement|Sitemap|About US| Contact US: help@patsnap.com