mems device, mems temperature sensor and respective manufacturing methods
A manufacturing method and device technology, applied in the field of MEMS temperature sensors and MEMS devices, can solve the problems of high cost, increased cantilever beam root fracture, complex structure of MEMS temperature sensors, etc., and achieve the effect of avoiding breakage
- Summary
- Abstract
- Description
- Claims
- Application Information
AI Technical Summary
Problems solved by technology
Method used
Image
Examples
Embodiment Construction
[0078] As mentioned in the background art, the performance of MEMS devices and MEMS temperature sensors in the prior art needs to be improved and the structure needs to be simplified. In order to solve the above technical problems, the present invention provides MEMS devices and manufacturing methods thereof, MEMS temperature sensors and manufacturing methods thereof to solve them.
[0079] Specifically, for the MEMS device, a folded structure is added to the connection between the fixed part and the movable part of the cantilever beam to strengthen the connection of the movable part of the cantilever beam to prevent it from breaking.
[0080] For the MEMS temperature sensor, a strain gauge with a different thermal expansion coefficient is placed on the lower surface of the cantilever beam movable part, so that during the measurement process, the cantilever beam movable part is warped and deformed due to the difference in thermal expansion coefficient and the strain gauge, and ...
PUM
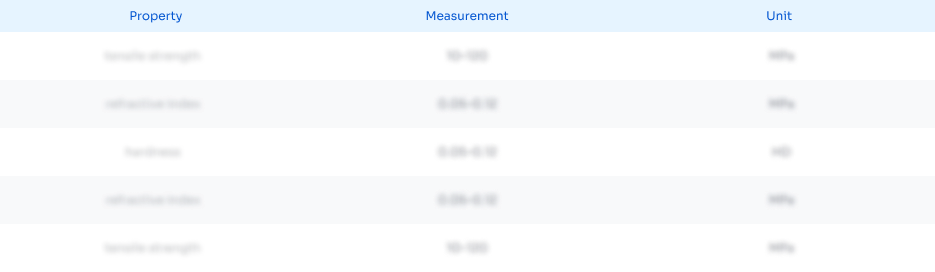
Abstract
Description
Claims
Application Information

- Generate Ideas
- Intellectual Property
- Life Sciences
- Materials
- Tech Scout
- Unparalleled Data Quality
- Higher Quality Content
- 60% Fewer Hallucinations
Browse by: Latest US Patents, China's latest patents, Technical Efficacy Thesaurus, Application Domain, Technology Topic, Popular Technical Reports.
© 2025 PatSnap. All rights reserved.Legal|Privacy policy|Modern Slavery Act Transparency Statement|Sitemap|About US| Contact US: help@patsnap.com