Digital direct jet printing process of polyester fabric
A technology of digital direct injection and processing technology, applied in the field of polyester fabric processing, can solve the problems of high paper consumption and environmental impact, and achieve the effect of saving resources and reducing consumption.
- Summary
- Abstract
- Description
- Claims
- Application Information
AI Technical Summary
Problems solved by technology
Method used
Examples
Embodiment 1
[0018] Example 1: A digital direct-injection printing process for polyester fabrics, including the following steps: (1) Computer color separation: color separation and toning of the pattern in the computer; (2) Fabric pretreatment: polyester fabric After adding the chemical fiber cloth direct spray pretreatment liquid for color enhancement, it is dried by a dryer at a drying temperature of 180°C; (3) Digital printing: The dispersed ink is sprayed onto the polyester fabric by a digital direct printing machine (4) High-temperature fixation: the polyester fabric after printing is fixed by a steaming machine, the fixation temperature is 190℃, and the time is 30min.
[0019] At the same time, the chemical fiber cloth direct injection pretreatment liquid is a high-performance chemical fiber cloth direct injection special pretreatment liquid purchased from Huanghua City Caizhiyuan Inkjet Technology Co., Ltd. In terms of weight percentage, the disperse ink consists of the following: disp...
Embodiment 2
[0021] The difference between Example 2 and Example 1 is that in step (2) the fabric pretreatment, the drying temperature of the polyester fabric is 185°C; in the step (4) high temperature fixing, the fixing temperature is 205°C. The increase of the fixing temperature increases the diffusion speed of the disperse dye toward the inside of the polyester fiber, which makes the surface of the polyester fabric have better color fastness after fixing.
[0022] At the same time, in terms of weight percentage, the disperse ink consists of the following components: disperse dye 15%; ethylene glycol 12.5%; diethylene glycol 12.5%; surfactant 0.1%; antifungal agent 0.3%; defoamer 0.5%; Ionized water balance. The anti-mold agent is phenol, and the defoaming agent is emulsified silicone oil.
Embodiment 3
[0023] Embodiment 3 differs from embodiment 1 in that in step (2) the fabric pretreatment, the drying temperature of the polyester fabric is 190°C; in step (4) the high-temperature fixing, the fixing temperature is 220°C.
[0024] At the same time, in terms of weight percentage, the disperse ink is composed of the following components: disperse dye 20%; ethylene glycol 15%; diethylene glycol 15%; surfactant 0.1%; antifungal agent 0.1%; defoamer 0.5%; Ionized water balance. The anti-mold agent is phenol, and the defoaming agent is emulsified silicone oil.
PUM
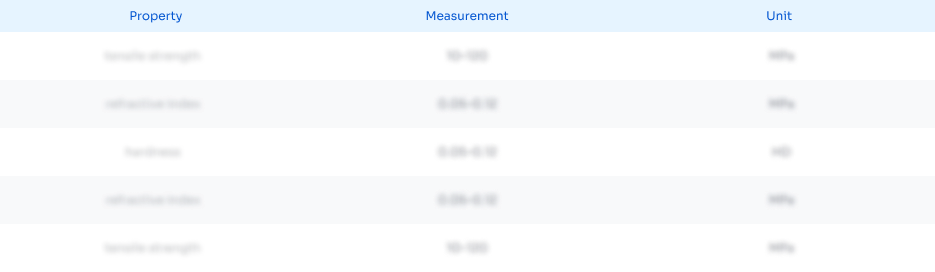
Abstract
Description
Claims
Application Information

- R&D Engineer
- R&D Manager
- IP Professional
- Industry Leading Data Capabilities
- Powerful AI technology
- Patent DNA Extraction
Browse by: Latest US Patents, China's latest patents, Technical Efficacy Thesaurus, Application Domain, Technology Topic, Popular Technical Reports.
© 2024 PatSnap. All rights reserved.Legal|Privacy policy|Modern Slavery Act Transparency Statement|Sitemap|About US| Contact US: help@patsnap.com