Plastic material forming, cooling and cutting system
A technology for plastic profiles and cutting systems, applied in the fields of plastic profile forming, cutting systems, and cooling, can solve problems such as cluttered layout, many equipment, and profile deformation.
- Summary
- Abstract
- Description
- Claims
- Application Information
AI Technical Summary
Problems solved by technology
Method used
Image
Examples
Embodiment Construction
[0013] Below in conjunction with all accompanying drawings the present invention will be further described, and preferred embodiment of the present invention is: see appended figure 1 to attach Figure 4 , the plastic profile forming, cooling and cutting system described in the present embodiment includes an extruder 80, the outlet of the extruder 80 is provided with a conveyor belt 81, and the output end of the conveyor belt 81 is provided with a traction conveying mechanism 82, and the traction conveying mechanism The output end of 82 is provided with a deviation correction mechanism 83, the output end of the deviation correction mechanism 83 is provided with a cooling forming mechanism 84, the output end of the cooling forming mechanism 84 is provided with an air cooling mechanism 85, and the output end of the air cooling mechanism 85 is provided with a fixed-length cutting mechanism 86; The traction conveying mechanism 82 comprises an organic base 41, an upper conveyor bel...
PUM
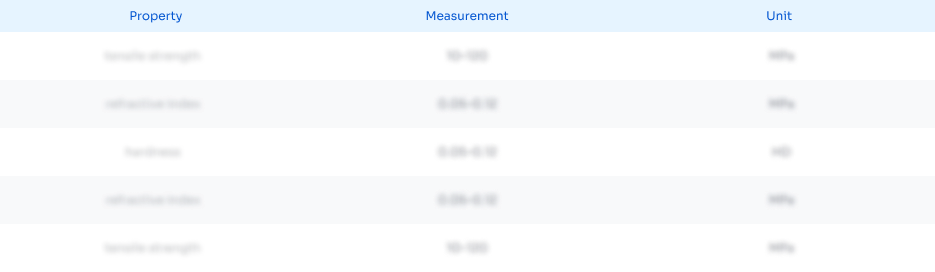
Abstract
Description
Claims
Application Information

- Generate Ideas
- Intellectual Property
- Life Sciences
- Materials
- Tech Scout
- Unparalleled Data Quality
- Higher Quality Content
- 60% Fewer Hallucinations
Browse by: Latest US Patents, China's latest patents, Technical Efficacy Thesaurus, Application Domain, Technology Topic, Popular Technical Reports.
© 2025 PatSnap. All rights reserved.Legal|Privacy policy|Modern Slavery Act Transparency Statement|Sitemap|About US| Contact US: help@patsnap.com