Car audio panel injection mold
A car audio and injection molding technology, which is applied to home appliances, other home appliances, household components, etc., can solve the problems of difficult control of processing size precision, high processing difficulty, waste of raw materials for injection molding aggregates, etc., and achieve saving mold steel materials , Improve injection molding efficiency and reduce material cost
- Summary
- Abstract
- Description
- Claims
- Application Information
AI Technical Summary
Problems solved by technology
Method used
Image
Examples
Embodiment Construction
[0023] Below in conjunction with accompanying drawing, the present invention will be further described (be described below with the direction that fixed mold seat plate 11 is positioned on the whole mould).
[0024] as figure 1 , figure 2 Take the car audio panel plastic part shown as an example, the through hole and the through groove on the plastic part are provided with the groove wall and the hole wall extending toward the inner side of the panel, and the round through hole is provided with a rib separating the keys. The inner side of the top panel, the inner side of the side panel and the inner side of the bottom panel are respectively provided with a snap-in structure, a buckle and a claw, and a plurality of mounting hole columns, limit thimbles and spacer grooves are also provided on the inner surface of the plastic part. , the overall shape and structure are more complex, and it is not easy to demould.
[0025] In order to improve production efficiency, one mold wit...
PUM
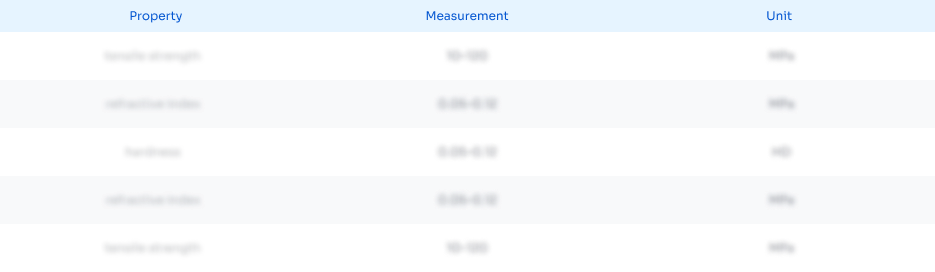
Abstract
Description
Claims
Application Information

- R&D
- Intellectual Property
- Life Sciences
- Materials
- Tech Scout
- Unparalleled Data Quality
- Higher Quality Content
- 60% Fewer Hallucinations
Browse by: Latest US Patents, China's latest patents, Technical Efficacy Thesaurus, Application Domain, Technology Topic, Popular Technical Reports.
© 2025 PatSnap. All rights reserved.Legal|Privacy policy|Modern Slavery Act Transparency Statement|Sitemap|About US| Contact US: help@patsnap.com