Industrial mechanical arm precision calibrating method based on collaborative Kriging
A technology of collaborative kriging and industrial machinery, applied in the field of robotics, can solve problems such as expensive and troublesome kinematic models, and achieve the effect of simple method, good versatility, and improved operation accuracy
- Summary
- Abstract
- Description
- Claims
- Application Information
AI Technical Summary
Problems solved by technology
Method used
Image
Examples
Embodiment approach
[0020] see figure 1 , the device used in the present invention is made up of industrial mechanical arm, laser tracker and target ball. The target ball is fixed at the end of the industrial robot arm.
[0021] The steps of the method of the present invention are described in detail below.
[0022] The specific implementation steps of the inventive method are as follows:
[0023] Step 1: Set up the laser tracker on the ground so that the movement space of the industrial robot arm is included in the measurement range of the laser tracker, and install the target ball at the end of the industrial robot arm;
[0024] Step 2: Use the target ball as the center point of the tool, and obtain the coordinates of the target ball relative to the end coordinate system of the industrial manipulator arm through the calibration method of the tool center point of the industrial manipulator;
[0025] Step 3: Mark the coordinate system of the laser tracker to the base of the industrial robot ar...
PUM
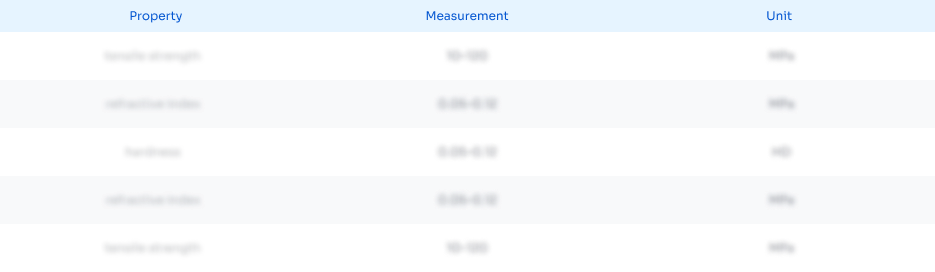
Abstract
Description
Claims
Application Information

- R&D
- Intellectual Property
- Life Sciences
- Materials
- Tech Scout
- Unparalleled Data Quality
- Higher Quality Content
- 60% Fewer Hallucinations
Browse by: Latest US Patents, China's latest patents, Technical Efficacy Thesaurus, Application Domain, Technology Topic, Popular Technical Reports.
© 2025 PatSnap. All rights reserved.Legal|Privacy policy|Modern Slavery Act Transparency Statement|Sitemap|About US| Contact US: help@patsnap.com