Field calibration system for magnetoelectric sensor
A magnetoelectric sensor and on-site calibration technology, applied in the direction of using electric devices, using electromagnetic means, instruments, etc., can solve the problem that it cannot be used as a judgment sensor, cannot guarantee the signal-to-noise ratio of high-frequency bands, and has poor anti-interference ability in high-frequency parts and other problems, to achieve the effect of simple structure, elimination of calibration error, and convenient portability
- Summary
- Abstract
- Description
- Claims
- Application Information
AI Technical Summary
Problems solved by technology
Method used
Image
Examples
Embodiment Construction
[0025] The present invention will be described in further detail below in conjunction with the examples and the accompanying drawings, but the embodiments of the present invention are not limited thereto.
[0026] see figure 1 , which is a connection block diagram of the magnetoelectric sensor calibration system of the present invention.
[0027] The invention provides an on-site calibration system for a magnetoelectric sensor, which includes a digital acquisition instrument 1, a calibration circuit 2, a signal processing device 3 and a magnetoelectric sensor 4 to be calibrated. The digital acquisition instrument 1 is respectively connected with the calibration circuit 2, the magnetoelectric sensor 4 and the signal processing device. The digital acquisition instrument 1 collects the signals of the calibration circuit 2 and the magnetoelectric sensor 4 , sends them to the signal processing device 3 for processing, and finally calculates the electrical sensitivity of the magnet...
PUM
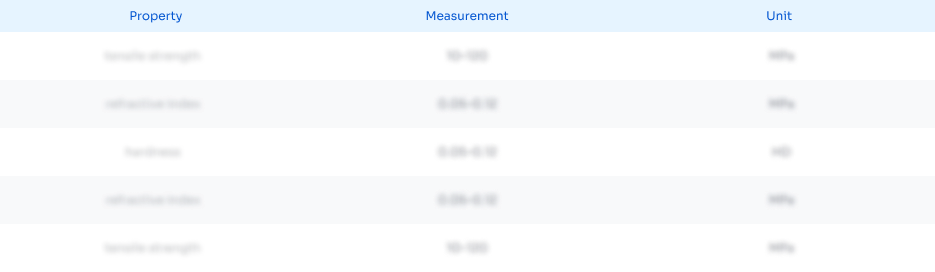
Abstract
Description
Claims
Application Information

- R&D Engineer
- R&D Manager
- IP Professional
- Industry Leading Data Capabilities
- Powerful AI technology
- Patent DNA Extraction
Browse by: Latest US Patents, China's latest patents, Technical Efficacy Thesaurus, Application Domain, Technology Topic, Popular Technical Reports.
© 2024 PatSnap. All rights reserved.Legal|Privacy policy|Modern Slavery Act Transparency Statement|Sitemap|About US| Contact US: help@patsnap.com