Rotary blowing equipment and method for molten iron desulphurization
A technology of rotary injection and molten iron desulfurization, applied in the field of iron and steel smelting molten iron pretreatment, can solve the problems of high consumption of desulfurization agent, low desulfurization efficiency, complex metallurgical equipment, etc., to improve production safety, good equipment power conditions, and desulfurization powder Low consumption effect
- Summary
- Abstract
- Description
- Claims
- Application Information
AI Technical Summary
Problems solved by technology
Method used
Image
Examples
Embodiment 1
[0046] The desulfurization production line of a steel factory in Northeast China was built in 1999, which belongs to the injection method desulfurization. In recent years, with the increase of the proportion of high-quality steel, the requirements for deep desulfurization of molten iron have been increasing day by day. The original spray desulfurization method can no longer meet the new smelting conditions and requirements. Therefore, after 2010, the desulfurization production lines in the new work area of the steel plant all adopt the KR method. , but the transformation of the original injection method production line is very difficult, the biggest problem is the small space, and the transformation changes greatly and the investment is also large, so it cannot be implemented.
[0047] Later, the molten iron desulfurization spinning rotor method (spinning rotor) of the present invention, hereinafter referred to as the SR method, was adopted. With only a little reinforcement ...
PUM
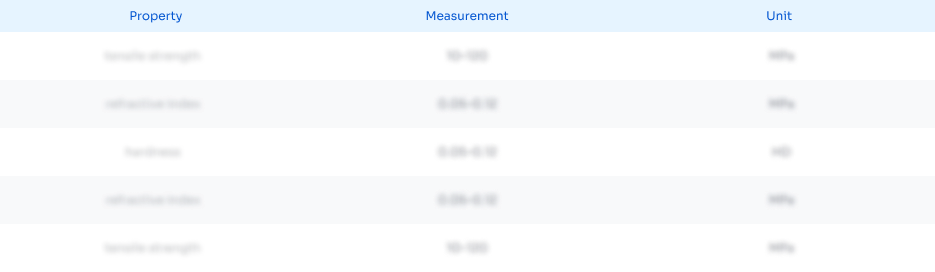
Abstract
Description
Claims
Application Information

- R&D
- Intellectual Property
- Life Sciences
- Materials
- Tech Scout
- Unparalleled Data Quality
- Higher Quality Content
- 60% Fewer Hallucinations
Browse by: Latest US Patents, China's latest patents, Technical Efficacy Thesaurus, Application Domain, Technology Topic, Popular Technical Reports.
© 2025 PatSnap. All rights reserved.Legal|Privacy policy|Modern Slavery Act Transparency Statement|Sitemap|About US| Contact US: help@patsnap.com