Method and device for controlling oxygen concentration of optical fiber curing oven
A technology of oxygen concentration and control method, applied in the direction of ratio control, control/regulation system, non-electric variable control, etc., can solve the problems of inability to monitor oxygen concentration and multi-range adjustment, so as to improve the curing effect, increase the oxygen content, The effect of increasing the oxygen concentration
- Summary
- Abstract
- Description
- Claims
- Application Information
AI Technical Summary
Problems solved by technology
Method used
Image
Examples
Embodiment 1
[0044] In order to control the oxygen concentration in the optical fiber curing furnace, this embodiment discloses a method for controlling the oxygen concentration in the optical fiber curing furnace, including:
[0045] Connect the first nitrogen pipe to the upper joint of the optical fiber curing furnace, feed nitrogen into the first nitrogen pipe, and discharge the nitrogen gas fed into the first nitrogen pipe from the upper end of the upper joint;
[0046] Connect the second nitrogen pipe to the lower joint of the optical fiber curing furnace, feed nitrogen into the second nitrogen pipe, and discharge the nitrogen gas fed into the second nitrogen pipe from the lower end of the lower joint;
[0047] Connect the third nitrogen pipe to one of the joints of the optical fiber curing furnace, connect the exhaust pipe to the other joint, feed nitrogen into the third nitrogen pipe, and make the nitrogen fed into the third nitrogen pipe flow from one end of the quartz tube to the ...
Embodiment 2
[0057] Such as figure 1 As shown, the optical fiber preform 1 is melted after being heated at a high temperature of 2000-2200°C in the drawing furnace 2. After coming out of the drawing furnace 2, it is annealed through the annealing tube 3. At this time, the temperature is about 900-1200°C, and then passes through the cooling tube 5. Lower the temperature until the process temperature required for coating is 30-80°C. After the optical fiber 4 is cooled, it enters the coating system 6 for coating coating. After coming out of the coating system 6, the surface of the optical fiber 4 will be coated with a liquid coating, which needs to enter the optical fiber curing furnace 7 for curing. According to the difference in process and line speed, 5 to 8 curing furnaces are required, and the optical fiber 4 is collected after being pulled by the pulling device 12 after being cured.
[0058] In order to control the oxygen concentration in the optical fiber curing furnace 7, this embodi...
PUM
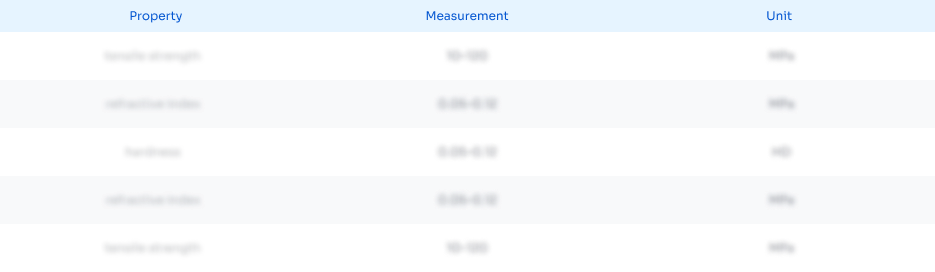
Abstract
Description
Claims
Application Information

- Generate Ideas
- Intellectual Property
- Life Sciences
- Materials
- Tech Scout
- Unparalleled Data Quality
- Higher Quality Content
- 60% Fewer Hallucinations
Browse by: Latest US Patents, China's latest patents, Technical Efficacy Thesaurus, Application Domain, Technology Topic, Popular Technical Reports.
© 2025 PatSnap. All rights reserved.Legal|Privacy policy|Modern Slavery Act Transparency Statement|Sitemap|About US| Contact US: help@patsnap.com