Control device for automatic welding for grid plate of robot, and working method thereof
A control device and automatic welding technology, applied in auxiliary devices, manufacturing tools, welding equipment, etc., can solve problems such as difficult process completion, high cost, and insufficient technology, and achieve the effect of simple process and improved quality
- Summary
- Abstract
- Description
- Claims
- Application Information
AI Technical Summary
Problems solved by technology
Method used
Image
Examples
Embodiment
[0040] In this embodiment, a robot automatic welding grid plate control device includes: a base 1, a mechanical arm 2, a wrist joint 3, a touch screen 4, and a control system 5;
[0041] The relationship between the above components is as follows:
[0042] Wherein, the wrist joint 3 is provided with an industrial camera 6 and a welding gun 7, the mechanical arm 2 is provided on the base 1, the wrist joint 3 is provided at the end of the mechanical arm 2, and the touch screen 4 is provided On the support frame of the base 1, the mechanical arm 2, the wrist joint 3, the touch screen 4 and the industrial camera 6 are all connected to the control system 5, and the control system 5 is provided with an electric control box.
[0043] In this embodiment, the mechanical arm 2 is composed of multiple sets of mechanical shafts, and each mechanical shaft is movably connected, and the mechanical arm 2 is connected to the base 1 through a rotating shaft 8.
[0044] The control system 5 described in...
Embodiment 2
[0050] In this embodiment, a robot automatic welding grid plate control device includes: a base 1, a mechanical arm 2, a wrist joint 3, a touch screen 4, and a control system 5;
[0051] The relationship between the above components is as follows:
[0052] Wherein, the wrist joint 3 is provided with an industrial camera 6 and a welding gun 7, the mechanical arm 2 is provided on the base 1, the wrist joint 3 is provided at the end of the mechanical arm 2, and the touch screen 4 is provided On the support frame of the base 1, the mechanical arm 2, the wrist joint 3, the touch screen 4 and the industrial camera 6 are all connected to the control system 5, and the control system 5 is provided with an electric control box.
[0053] In this embodiment, the mechanical arm 2 is composed of multiple sets of mechanical shafts, and each mechanical shaft is movably connected, and the mechanical arm 2 is connected to the base 1 through a rotating shaft 8.
[0054] The control system 5 described in...
PUM
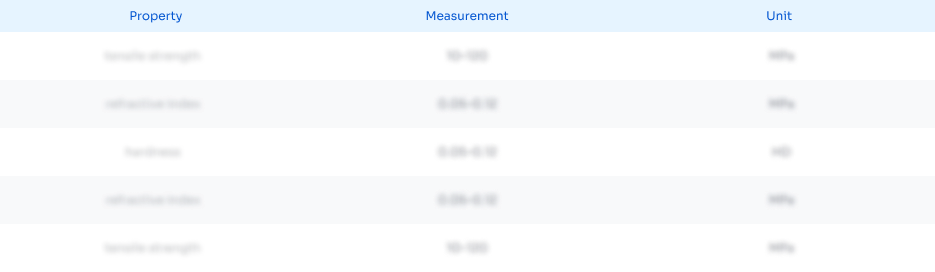
Abstract
Description
Claims
Application Information

- Generate Ideas
- Intellectual Property
- Life Sciences
- Materials
- Tech Scout
- Unparalleled Data Quality
- Higher Quality Content
- 60% Fewer Hallucinations
Browse by: Latest US Patents, China's latest patents, Technical Efficacy Thesaurus, Application Domain, Technology Topic, Popular Technical Reports.
© 2025 PatSnap. All rights reserved.Legal|Privacy policy|Modern Slavery Act Transparency Statement|Sitemap|About US| Contact US: help@patsnap.com