Synchronous punching device in internal high-pressure forming mold
A technology of punching device and forming die, which is applied in the field of pipe fittings processing, can solve the problems of low processing efficiency, increase of production cost, and increase of clamping times, and achieve the effects of good flexibility of use, improvement of reliability and processing accuracy
- Summary
- Abstract
- Description
- Claims
- Application Information
AI Technical Summary
Problems solved by technology
Method used
Image
Examples
Embodiment Construction
[0023] Such as Figure 1-4 as shown, figure 1 It is a structural schematic diagram of a synchronous punching device in an internal high pressure forming die proposed by the present invention, figure 2 It is a structural schematic diagram of the cooperation between the insert and the rack of a synchronous punching device in an internal high pressure forming die proposed by the present invention, image 3 for figure 1 The speed curves calculated by the simulation calculation of the first punch and the second punch, Figure 4 for figure 1 Displacement curves obtained from simulation calculations of the first punch and the second punch.
[0024] refer to figure 1 and 2 , a synchronous punching device in an internal high pressure forming mold proposed by the present invention, comprising: a mold assembly 1, a punching assembly, a liquid inlet mechanism, and a driving mechanism 7;
[0025] The mold assembly 1 has a mold cavity for accommodating pipe fittings to be processed,...
PUM
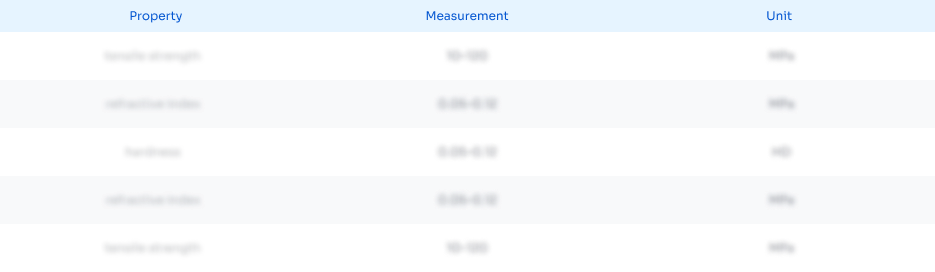
Abstract
Description
Claims
Application Information

- Generate Ideas
- Intellectual Property
- Life Sciences
- Materials
- Tech Scout
- Unparalleled Data Quality
- Higher Quality Content
- 60% Fewer Hallucinations
Browse by: Latest US Patents, China's latest patents, Technical Efficacy Thesaurus, Application Domain, Technology Topic, Popular Technical Reports.
© 2025 PatSnap. All rights reserved.Legal|Privacy policy|Modern Slavery Act Transparency Statement|Sitemap|About US| Contact US: help@patsnap.com