Semi-polished ceramic glazed tile with fluorescent effect and manufacturing method thereof
A manufacturing method and technology of ceramic glaze, applied in the field of ceramic construction, can solve the problems of unstable properties and unstable components of fluorescent glaze, and achieve stable product quality, good fluorescent effect, and meet the effects of individualization and diversification.
- Summary
- Abstract
- Description
- Claims
- Application Information
AI Technical Summary
Problems solved by technology
Method used
Image
Examples
Embodiment 1
[0072] First, 35kg of quartz, 15kg of feldspar, 5kg of hard clay and 25kg of plastic clay are mixed and stirred evenly, then 20kg of lime powder is added and stirred evenly, and then the raw materials are put into a ball mill for ball milling and iron removal until the fineness of the raw materials Reach 2.0% of 250 mesh sieve. Then use the spray drying tower to spray the raw material into powder and control the moisture content of the powder to 4.5%, then the powder is molded by a press with a pressure of 32MPa to form a green body with a specification of 600×300mm, and then the green body Put it into a biscuit kiln and biscuit at a temperature of 1500° C. for 2 hours to obtain a biscuit, which is set aside.
[0073] Mix 3kg of fluorescent dry granules and 7kg of printing paste and mechanically stir evenly to make a glaze slurry of fluorescent dry granules for later use, wherein the chemical composition mass percentage of fluorescent dry granules is: SiO 2 70.49%, Al 2 o ...
Embodiment 2
[0077] First, 35kg of quartz, 15kg of feldspar, 5kg of hard clay and 25kg of plastic clay are mixed and stirred evenly, then 20kg of lime powder is added and stirred evenly, and then the raw materials are put into a ball mill for ball milling and iron removal until the fineness of the raw materials Reach 2.0% of 250 mesh sieve. Then use the spray drying tower to spray the raw material into powder and control the moisture content of the powder to 4.5%, then the powder is molded by a press with a pressure of 32MPa to form a green body with a specification of 600×300mm, and then the green body Put it into a biscuit kiln and biscuit at a temperature of 1500° C. for 2 hours to obtain a biscuit, which is set aside.
[0078] Mix 3kg of fluorescent dry granules and 7kg of printing paste and mechanically stir evenly to make a glaze slurry of fluorescent dry granules for later use, wherein the chemical composition mass percentage of fluorescent dry granules is: SiO 2 70.49%, Al 2 o ...
Embodiment 3
[0082] First, 35kg of quartz, 15kg of feldspar, 5kg of hard clay and 25kg of plastic clay are mixed and stirred evenly, then 20kg of lime powder is added and stirred evenly, and then the raw materials are put into a ball mill for ball milling and iron removal until the fineness of the raw materials Reach 2.0% of 250 mesh sieve. Then use the spray drying tower to spray the raw material into powder and control the moisture content of the powder to 4.5%, then the powder is molded by a press with a pressure of 32MPa to form a green body with a specification of 600×300mm, and then the green body Put it into a biscuit kiln and biscuit at a temperature of 1500° C. for 2 hours to obtain a biscuit, which is set aside.
[0083] Mix 3kg of fluorescent dry granules and 7kg of printing paste and mechanically stir evenly to make a glaze slurry of fluorescent dry granules for later use, wherein the chemical composition mass percentage of fluorescent dry granules is: SiO 2 70.49%, Al 2 o 3 ...
PUM
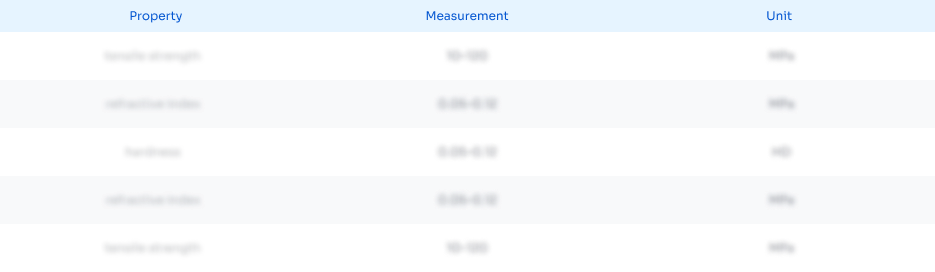
Abstract
Description
Claims
Application Information

- R&D
- Intellectual Property
- Life Sciences
- Materials
- Tech Scout
- Unparalleled Data Quality
- Higher Quality Content
- 60% Fewer Hallucinations
Browse by: Latest US Patents, China's latest patents, Technical Efficacy Thesaurus, Application Domain, Technology Topic, Popular Technical Reports.
© 2025 PatSnap. All rights reserved.Legal|Privacy policy|Modern Slavery Act Transparency Statement|Sitemap|About US| Contact US: help@patsnap.com