Ethylene copolymer having excellent processability
A technology of ethylene copolymer and olefin copolymerization, which is applied in the field of ethylene copolymer and can solve the problems of impact strength, tear strength drop, low DRI, etc.
- Summary
- Abstract
- Description
- Claims
- Application Information
AI Technical Summary
Problems solved by technology
Method used
Image
Examples
manufacture example
[0111] Non-halogenated monocyclopentadienyl group 4 metal compound (dimethylsilylene(tert-butylamino)-(tetramethylcyclopentadienyl)-titanium dibenzyl:Me 2 Si(NtBu)(Cp*)Ti(Bn) 2 )Synthesis
[0112] Measure out Ti(CH 2 Ph) 4 5.2mmol and dimethylsilylene (t-butylamino)-(tetramethylcyclopentadienyl) (Dimethylsilylene (t-butylamido) (tetramethycyclopentadienyl)) 4.0mmol, injected with Schlenk Line ) 50mL of refined toluene, which was completely dissolved. The temperature of the reactor blocked from sunlight was raised to 60° C. and allowed to react for 12 hours.
[0113] The reaction was dried in vacuo. The dried reaction was extracted again with pentane, which was dried again in vacuo to finally give Me 2 Si(NtBu)(Cp*)Ti(Bn) 2 . The yield was greater than 90%. The structure of the compound through 1 Confirmed by H NMR.
[0114] 1 H NMR (400MHz, C6D6) 7.16 (Ph, 4H, d), 6.95 (Ph, 4H, t), 6.90 (Ph, 2H, t), 2.58 (CH 2 Ph,2H,d),2.25(CH 2 Ph,2H,d),1.81(C 5 Me 4 ,6H,s),1....
Embodiment 1
[0116] [Manufacture of Metallocene Supported Catalyst]
[0117] For trade name XPO-2402 (Grace Company (USA), average particle size ~ 50 μ m, surface area 300 m 2 / g, fine pore volume 1.6ml / g, OH concentration 1mmol / g) dehydrated silica, quantitatively 500g under anhydrous conditions, stirred with toluene to form a slurry state. It was injected into a 10 L reactor with stirrer and condenser. The methylaluminoxane solution (10% by weight) (methylaluminoxane / g silica=15 mmol / g silica) was quantified with a graduated cylinder, and injected into the reactor. Then, the temperature of the reactor was raised to 110° C. while stirring. The loading reaction was allowed to proceed for 90 minutes at this temperature. After the reaction was completed, the reactant was placed, and the upper solution was decanted. Inject 500 mL of toluene solution, wash the reactant, place the reactant, and decant the upper solution. This operation was repeated twice.
[0118] A quantitative amount of...
Embodiment 2
[0148] In Example 1, no ethylenebis(4,5,6,7-tetrahydroindenyl)zirconium dichloride (Et(THI) 2 ZrCl 2 ) as a metallocene catalyst component, a catalyst was produced using bis(n-butylcyclopentadienyl) zirconium dichloride under the same conditions as in Example 1, and polymerization was carried out under the same conditions as in Example 1.
PUM
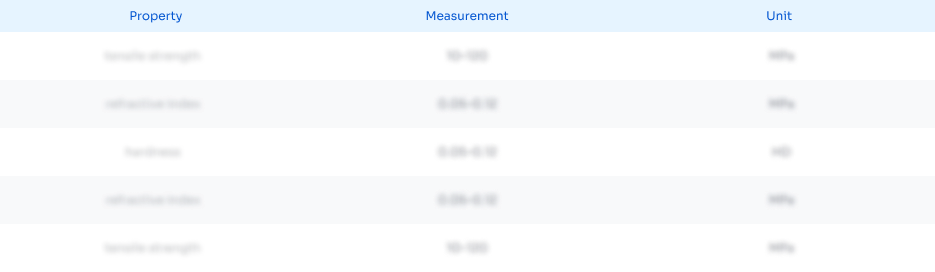
Abstract
Description
Claims
Application Information

- R&D
- Intellectual Property
- Life Sciences
- Materials
- Tech Scout
- Unparalleled Data Quality
- Higher Quality Content
- 60% Fewer Hallucinations
Browse by: Latest US Patents, China's latest patents, Technical Efficacy Thesaurus, Application Domain, Technology Topic, Popular Technical Reports.
© 2025 PatSnap. All rights reserved.Legal|Privacy policy|Modern Slavery Act Transparency Statement|Sitemap|About US| Contact US: help@patsnap.com