Non-linear industrial process fault detection method based on Bayes kernel slow feature analysis
A fault detection and industrial process technology, applied in electrical testing/monitoring, testing/monitoring control systems, instruments, etc., can solve problems such as inability to accurately extract non-linear characteristic information of data
- Summary
- Abstract
- Description
- Claims
- Application Information
AI Technical Summary
Problems solved by technology
Method used
Image
Examples
Embodiment 1
[0089] Embodiment 1: A nonlinear numerical system is taken as an example for illustration. simulates a system with three monitored variables x 1 ,x 2 ,x 3 The nonlinear numerical system of , its mathematical description is as follows:
[0090]
[0091] where e 1 ,e 2 ,e 3 ∈N(0,0.01) represents three independent noise variables, t∈[0,2] is a uniformly distributed random variable, and the output of the system [x 1 ,x 2 ,x 3] as a process monitoring variable. 300 samples were simulated under normal operating conditions as shown in equation (25) as training data for modeling. In order to generate fault data, at the 51st time in the simulation process, the variable x 1 Add ramp fault F1 and keep fault F1 until the end of the simulation at time 300.
[0092] The fault detection method for the above nonlinear numerical system includes the following steps:
[0093] (1) Collect the normal operating condition data of the nonlinear numerical system as the training data X ...
Embodiment 2
[0162] Embodiment two: Take the continuous stirred reactor (CSTR) system as an example, see Figure 4 , in the CSTR system, material A enters the reactor, a first-order irreversible chemical reaction occurs, material B is generated, heat is released, and the reactor is cooled by the jacketed coolant outside. In order to ensure the normal operation of the process, a cascade control system is adopted Control the liquid level and temperature of the reactor.
[0163] According to the process mechanism, the dynamic mechanism model of the CSTR system is established as follows:
[0164]
[0165]
[0166]
[0167]
[0168] In the formula, A is the cross-sectional area of the reactor, c A is the concentration of material A in the reactor, c AF is the concentration of material A in the feed, C p is the specific heat of the reactants, C pC is the coolant specific heat, E is the activation energy, h is the reactor liquid level, k 0 is the response factor, Q F Feed flow...
PUM
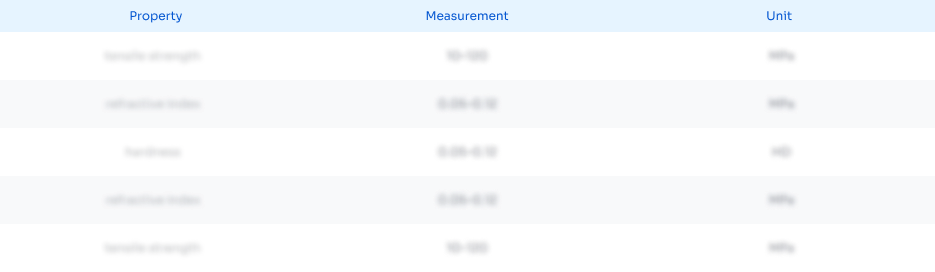
Abstract
Description
Claims
Application Information

- R&D
- Intellectual Property
- Life Sciences
- Materials
- Tech Scout
- Unparalleled Data Quality
- Higher Quality Content
- 60% Fewer Hallucinations
Browse by: Latest US Patents, China's latest patents, Technical Efficacy Thesaurus, Application Domain, Technology Topic, Popular Technical Reports.
© 2025 PatSnap. All rights reserved.Legal|Privacy policy|Modern Slavery Act Transparency Statement|Sitemap|About US| Contact US: help@patsnap.com