Unmanned aerial vehicle bridge bottom surface crack detection method and system
A crack detection and unmanned aerial vehicle technology, applied in control/adjustment systems, measuring devices, optical testing flaws/defects, etc., can solve problems such as systems that have not been implemented by anyone, and achieve low cost, high degree of automation, and high safety factor. Effect
- Summary
- Abstract
- Description
- Claims
- Application Information
AI Technical Summary
Problems solved by technology
Method used
Image
Examples
Embodiment Construction
[0050] The invention provides a method and system for detecting cracks on the bottom surface of an unmanned aerial vehicle bridge. In order to make the object, technical solution and effect of the present invention more clear and definite, the present invention will be further described in detail below with reference to the accompanying drawings.
[0051] The present invention mainly includes two parts, the UAV end and the image data processing end of the ground workstation. The hardware structure and module schematic diagram reference of the UAV figure 1 , the drone-side workflow is as follows figure 2 . The drone end of the crack detection system on the bottom surface of the drone bridge includes the following steps:
[0052]Step S100: rely on the airborne lidar and inertial measurement unit (IMU) to locate the unmanned aerial vehicle flying under the bridge;
[0053] Step S200: rely on the current position and attitude of the unmanned aerial vehicle obtained by S100, a...
PUM
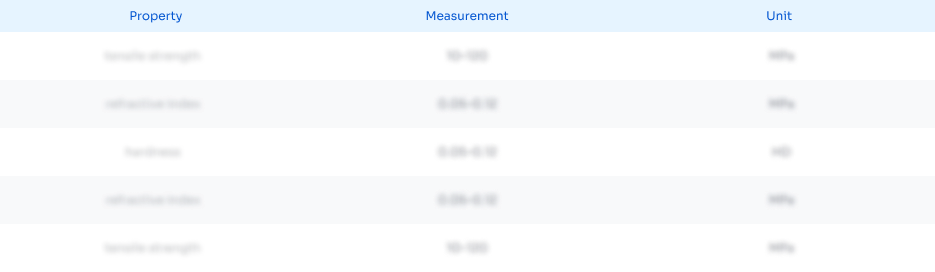
Abstract
Description
Claims
Application Information

- R&D
- Intellectual Property
- Life Sciences
- Materials
- Tech Scout
- Unparalleled Data Quality
- Higher Quality Content
- 60% Fewer Hallucinations
Browse by: Latest US Patents, China's latest patents, Technical Efficacy Thesaurus, Application Domain, Technology Topic, Popular Technical Reports.
© 2025 PatSnap. All rights reserved.Legal|Privacy policy|Modern Slavery Act Transparency Statement|Sitemap|About US| Contact US: help@patsnap.com