A kind of warm mix epoxy asphalt mixture and preparation method thereof
A technology for warm mix epoxy asphalt and epoxy asphalt, applied in the field of asphalt mixture, can solve the problem that the degree of reaction between intermediates and aromatic hydrocarbon oil, the depth of reaction is not easy to control, and the high temperature stability or low temperature cracking resistance of asphalt mixture is affected. Reduce the viscosity or elongation of asphalt at 60°C to achieve the effect of being beneficial to environmental protection and construction, improving Marshall stability and improving flexibility
- Summary
- Abstract
- Description
- Claims
- Application Information
AI Technical Summary
Problems solved by technology
Method used
Examples
Embodiment 1
[0051] (1) Preparation of warm mix agent
[0052] ①Weigh 100kg of coal gasification and then carry out the synthesis reaction of mixed alkanes, the carbon number of mixed alkanes is 30-60, heat the mixed alkanes to 480°C, add 0.3kg of catalyst anhydrous CuCl 2 , placed in a closed container, maintain this temperature and introduce 89 moles of chlorine gas, and feed nitrogen to keep the pressure of the reaction container at 3MPa, and react for 30 minutes to obtain intermediate-1;
[0053] ② Weigh 700kg of the oil extracted from the fourth line with an aromatics content of 70 wt%, and add 44.1kg of complex [Cu(NH 3 ) 4 ] SO 4 and 4.41kg of catalyst Cu, put in another airtight container and heated to 350°C, and react at this temperature for 180min at constant temperature to obtain aromatic hydrocarbon complexing component-1;
[0054] ③Add aromatic hydrocarbon complexing component-1 to the above-mentioned intermediate-1, make the temperature 400°C, fill with nitrogen to keep th...
Embodiment 2
[0066] (1) Preparation of warm mix agent
[0067] ① Weigh 350 kg of mixed alkanes obtained by synthesis reaction after coal gasification, the mixed alkanes have a carbon number of 30 to 130, heat the mixed alkanes to 400 ° C, add 3.15 kg of catalyst anhydrous MnCl 2 , placed in a closed container, kept at this temperature, introduced 116 moles of chlorine gas, and fed nitrogen to keep the pressure of the reaction container at 5 MPa, and reacted for 60 minutes to obtain intermediate-2;
[0068] ②Weigh 100kg of catalytic cracking oil slurry with an aromatics content of 63 wt%, and add 1.9kg of complex K 4 [Fe(CN) 6 ] and 0.19kg of catalyst Fe, packed in another airtight container and heated to 270 ° C, at this temperature constant temperature reaction 120min, to obtain the aromatic complex component-2;
[0069] ③Add aromatic hydrocarbon complexing component-2 to the above-mentioned intermediate-2, make the temperature 350°C, fill with nitrogen to keep the pressure at 4MPa, and...
Embodiment 3
[0081] (1) Preparation of warm mix agent
[0082] ①Weigh 100kg of mixed alkanes obtained by synthetic reaction with natural gas as raw material, the carbon number of mixed alkanes is 70-90, heat the mixed alkanes to 440°C, add 0.6kg of catalyst anhydrous NiCl 2 Put it in a closed container, maintain this temperature and introduce 31 moles of fluorine, and feed nitrogen to keep the pressure of the reaction container at 4MPa, and react for 45 minutes to obtain Intermediate-3;
[0083] ② Weigh 350kg of phenolic refined oil with an aromatics content of 78wt%, and add 16.4kg of complex [Ni(CO) 4 ] and 1.64kg of catalyst Ni were installed in another airtight container and heated to 310°C, and reacted at a constant temperature for 160min at this temperature to obtain aromatic hydrocarbon complexing component-3;
[0084] ③Add aromatic hydrocarbon complexing component-3 to the above-mentioned intermediate-3, make the temperature 375°C, fill with nitrogen to keep the pressure at 3MPa, ...
PUM
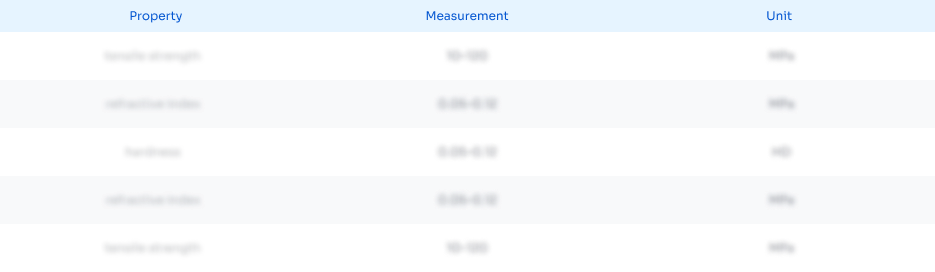
Abstract
Description
Claims
Application Information

- Generate Ideas
- Intellectual Property
- Life Sciences
- Materials
- Tech Scout
- Unparalleled Data Quality
- Higher Quality Content
- 60% Fewer Hallucinations
Browse by: Latest US Patents, China's latest patents, Technical Efficacy Thesaurus, Application Domain, Technology Topic, Popular Technical Reports.
© 2025 PatSnap. All rights reserved.Legal|Privacy policy|Modern Slavery Act Transparency Statement|Sitemap|About US| Contact US: help@patsnap.com