Fabric compounding device
A composite device and fabric technology, applied in lamination devices, layered products, lamination, etc., can solve problems such as deficiencies, and achieve the effects of reasonable overall structure, guaranteed quality, and good stability
- Summary
- Abstract
- Description
- Claims
- Application Information
AI Technical Summary
Problems solved by technology
Method used
Image
Examples
Embodiment 1
[0025] Embodiment 1: as figure 1 In the shown embodiment, a fabric compounding device includes a main frame 1, a finished material winding roller 21, a winding motor 21a for driving the finished material winding roller to rotate, and a lower layer feeding roller 3 wound with a lower layer of fabric And the upper layer feed roller 4 that is wound with upper layer fabric, described main frame is provided with the lower motor 3a that is used to drive the lower layer feed roller to rotate and the upper layer motor 4a that is used to drive the upper layer feed roller to rotate, and main frame is provided with material forming part , the material forming part includes the first shaping single roller 11, the second shaping single roller 12 and an ultrasonic welding machine 14 for compositely connecting each layer of fabric;
[0026] The ultrasonic welding machine is located between the first shaping single roller and the second shaping single roller. The main frame is equipped with a...
Embodiment 2
[0030] Embodiment 2: the basic structure and implementation mode of this embodiment are the same as embodiment 1, and its difference is, as Figure 2 to Figure 5 As shown in , there are two self-adjusting mechanisms 5 between the main frame and the winding frame, an adjusting transition roller 6 is arranged between the main frame and the two self-adjusting mechanisms, and the winding frame and the two self-adjusting mechanisms There is an adjustment transition roller between them, and two self-adjusting mechanisms are symmetrically arranged along a symmetrical plane, and the axis of the main roller for inspection is perpendicular to the said symmetrical plane. The air guide impeller 55, the air suction pipe 53 arranged on the adjustment frame and the fabric guide plate 54 used to stick to the bottom surface of the fabric to support the fabric, the axis of the cloth pulling wheel is horizontal and perpendicular to the axis of the main inspection roller;
[0031] In a self-adjus...
PUM
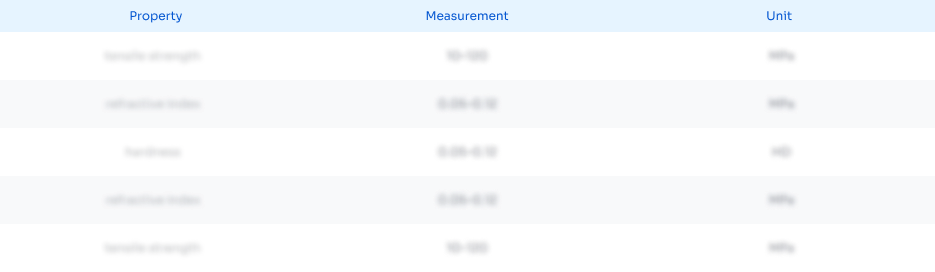
Abstract
Description
Claims
Application Information

- Generate Ideas
- Intellectual Property
- Life Sciences
- Materials
- Tech Scout
- Unparalleled Data Quality
- Higher Quality Content
- 60% Fewer Hallucinations
Browse by: Latest US Patents, China's latest patents, Technical Efficacy Thesaurus, Application Domain, Technology Topic, Popular Technical Reports.
© 2025 PatSnap. All rights reserved.Legal|Privacy policy|Modern Slavery Act Transparency Statement|Sitemap|About US| Contact US: help@patsnap.com