Flexible coupling module type blisk abrasive flow machining polishing clamp
A technology of coupling modules and integral blisks, which is applied in grinding/polishing equipment, surface polishing machine tools, grinding machines, etc., can solve the problems of poor uniformity of blade surface quality, unstable and continuous state of abrasive grain flow, and inconsistent spacing of gap flow channels, etc. problems, achieve the effect of reducing polishing cost, improving polishing accuracy and ensuring uniformity
- Summary
- Abstract
- Description
- Claims
- Application Information
AI Technical Summary
Problems solved by technology
Method used
Image
Examples
Embodiment Construction
[0018] An embodiment of the present invention will be described in detail below in conjunction with the accompanying drawings.
[0019] The embodiment of the invention is to polish a certain type of integral turbine blisk; as figure 1 , figure 2 As shown, it includes upper deflector 1, upper diverter 2, sealing ring 3, outer sleeve 4, lower diverter 5, lower deflector 6, buckle 7, restraint module 8, hoop 9, central shaft 10 , positioning pin 11, flat key 12, positioning pin 13; upper deflector 1 has a funnel-shaped bell-mouth flow channel; lower deflector 6 has a cone-shaped bell-mouth flow channel; There are center shaft mounting holes and distribution channels distributed in the circumferential direction; the upper deflector 1 is tightly connected with the upper deflector 2; the lower deflector 5 is tightly connected with the lower deflector 6; the turbine blades 14 generally include blades, the constraint module 8 is composed of sub-constraint modules with the same numb...
PUM
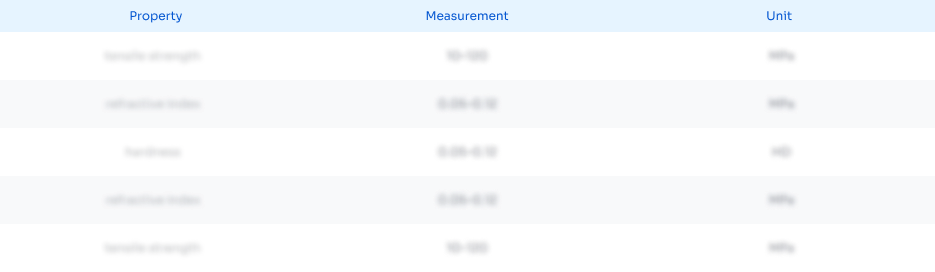
Abstract
Description
Claims
Application Information

- R&D
- Intellectual Property
- Life Sciences
- Materials
- Tech Scout
- Unparalleled Data Quality
- Higher Quality Content
- 60% Fewer Hallucinations
Browse by: Latest US Patents, China's latest patents, Technical Efficacy Thesaurus, Application Domain, Technology Topic, Popular Technical Reports.
© 2025 PatSnap. All rights reserved.Legal|Privacy policy|Modern Slavery Act Transparency Statement|Sitemap|About US| Contact US: help@patsnap.com