Multimode and multi-based unmanned aerial vehicle with tailed flying wing configuration
A technology of unmanned aerial vehicles and flying wings, applied in the field of flying wing unmanned aerial vehicles, can solve the problems of high research and development costs and difficulty in research and development, and achieve the effect of excellent aerodynamic characteristics, high effective loading factor, and high-efficiency integrated layout
- Summary
- Abstract
- Description
- Claims
- Application Information
AI Technical Summary
Problems solved by technology
Method used
Image
Examples
Embodiment 1
[0038] Such as figure 1 , 2 , Shown in 3, a kind of multi-mode multi-base unmanned aerial vehicle with tail flying wing layout, this aircraft comprises: the lifting body type fuselage 1 that longitudinal section is airfoil plane shape, the wing-body fusion type that is arranged on fuselage 1 both sides Main wing 2, upper wing 3, end wing 4, ducted propeller propulsion device 5 and vertical tail 6 arranged at the fuselage 1 tail. The main wing 2 arranged on both sides of the fuselage 1 is provided with an end wing 4 at the tip of the wing, and the upper parts of the two end wings 4 pass through the upper wing 3 arranged above the fuselage 1 and the rear wing arranged at the tail of the fuselage 1 respectively. The vertical tail 6 is connected, and the lower end of the vertical tail 6 is fixedly connected with the duct structure of the ducted propeller propulsion device 5 arranged at the fuselage 1 tail.
[0039] The unmanned aerial vehicle provided by the present invention ad...
Embodiment 2
[0041] According to an embodiment of the present invention, the multi-mode and multi-base unmanned aerial vehicle with tail flying wing layout provides a high-efficiency integrated energy power system design scheme, such as image 3 shown. Its features include:
[0042] The unmanned aerial vehicle adopts a layout form in which ducted fans 9 are arranged on both sides of the front of the fuselage 1 and before the center of gravity, so as to generate direct lifting force during the vertical take-off and landing phase. Such as Figure 4As shown, the ducted fans 9 on both sides of the fuselage 1 rotate in opposite directions, and are fixedly connected to both ends of the horizontal shaft 13 installed in the fuselage 1 . The ducted fan 9 is driven by two DC motors 15 turning in opposite directions and generates pulling force. The servo motor 12 installed in the fuselage 1 drives the worm gear 11 and meshes with the worm gear 14 on the horizontal shaft 13 . Both the servo motor ...
Embodiment 3
[0045] According to an embodiment of the present invention, the multi-mode multi-base unmanned aerial vehicle with tail flying wing layout, the system state under the vertical take-off and landing mode is as follows Figure 7 shown. Under the vertical take-off and landing working mode, the heavy oil piston type power unit 25 at the rear of the fuselage 1 remains in a "quiet" state. The ducted fan 9 on both sides of the fuselage 1 rotates to such as Figure 4 The shown vertical position rotates at a high speed and produces upward lifting force; the clutch 20 at the output end of the turbojet main shaft 19 is released, and the high-temperature and high-pressure gas expands in the exhaust nozzle 18 and produces a vertical upward thrust, that is, the lifting force , and the ducted fan 9 jointly generate enough lift to realize vertical take-off and landing under direct force control in the vertical direction. In addition, the jet thrust produced by the turbojet engine 10 can also...
PUM
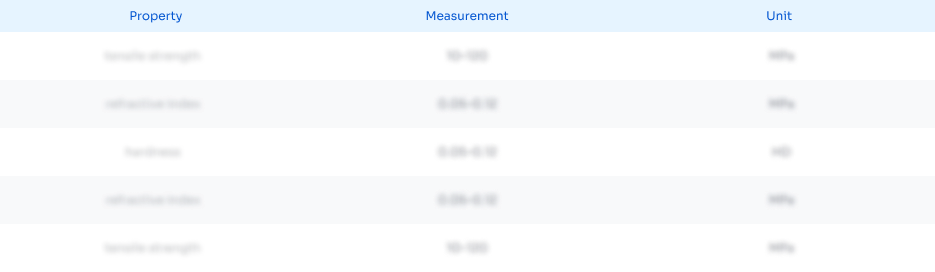
Abstract
Description
Claims
Application Information

- R&D
- Intellectual Property
- Life Sciences
- Materials
- Tech Scout
- Unparalleled Data Quality
- Higher Quality Content
- 60% Fewer Hallucinations
Browse by: Latest US Patents, China's latest patents, Technical Efficacy Thesaurus, Application Domain, Technology Topic, Popular Technical Reports.
© 2025 PatSnap. All rights reserved.Legal|Privacy policy|Modern Slavery Act Transparency Statement|Sitemap|About US| Contact US: help@patsnap.com