Rotary prism device driven by non-circular gears
A non-circular gear and rotating prism technology, applied in the field of precision optical scanning, can solve the problems of difficult cam profile curve design and processing, inability to drive the full circle rotation of the prism, affecting the deflection accuracy of the prism, etc., to ensure high-precision dynamic scanning. performance, reduced control requirements, and accurate transmission
- Summary
- Abstract
- Description
- Claims
- Application Information
AI Technical Summary
Problems solved by technology
Method used
Image
Examples
Embodiment 1
[0039] In this embodiment, two devices of the present invention are used, and the two prisms are arranged coaxially during installation to form a rotating double prism system. Below in conjunction with the accompanying drawings, taking a device of the present invention as an example, the structural principle and working process of the device of the present invention will be described in detail.
[0040] see figure 1 , in the rotating prism device, the rotating motor 15 drives a two-stage reduction system consisting of a pair of non-circular gears and a pair of cylindrical gears, and transmits the nonlinear motion relationship to the driven circular gear. The prism is rigidly coupled with the mirror frame assembly and the driven circular gear 8, therefore, the present invention can realize the precise rotational movement of the wedge-shaped prism 6 within the full circumference range.
[0041] see figure 1 , the prism and frame assembly includes a frame 4 , a prism washer 5 ,...
PUM
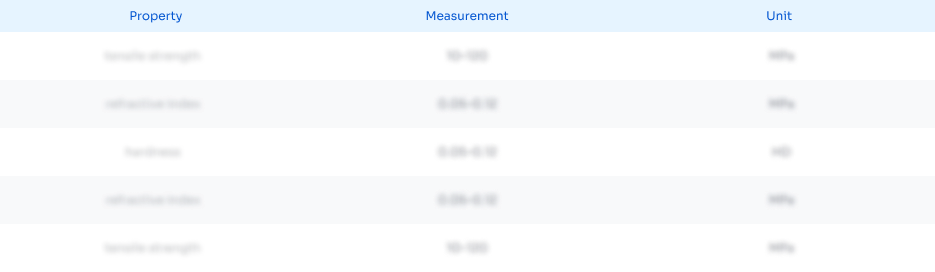
Abstract
Description
Claims
Application Information

- R&D
- Intellectual Property
- Life Sciences
- Materials
- Tech Scout
- Unparalleled Data Quality
- Higher Quality Content
- 60% Fewer Hallucinations
Browse by: Latest US Patents, China's latest patents, Technical Efficacy Thesaurus, Application Domain, Technology Topic, Popular Technical Reports.
© 2025 PatSnap. All rights reserved.Legal|Privacy policy|Modern Slavery Act Transparency Statement|Sitemap|About US| Contact US: help@patsnap.com