Brake baseplate machining fixture
A brake base plate and fixture technology, applied in the direction of manufacturing tools, metal processing equipment, metal processing machinery parts, etc., can solve the problems of high processing cost, low work efficiency, high labor intensity for changing models, etc., and achieves convenient use and simple structure. Effect
- Summary
- Abstract
- Description
- Claims
- Application Information
AI Technical Summary
Problems solved by technology
Method used
Image
Examples
Embodiment Construction
[0020] The brake bottom plate processing fixture is composed of a bottom plate 1, a mounting seat 2, a mounting plate 3, a support nail A4, a support nail B5, a positioning nail A6, a positioning nail B7, a pressing block 8, a pressing plate 9, a pressing screw 10 and a fastening screw 11. The bottom plate 1 is evenly distributed with strip-shaped sliding holes 15; the mounting plate 3 and the mounting seat 2 are arranged symmetrically to each other, and are fixedly connected to the strip-shaped sliding holes 15 through T-shaped bolts 16 respectively. After setting in this way, people can adjust the distance between the mounting plate 3 and the mounting base 2 according to the size of the brake base plate, so that the processing fixture is suitable for clamping various brake base plates.
[0021] The bottom ends of the mounting plate 3 and the mounting seat 2 are respectively provided with guide rails 25 ; the bottom plate 1 below the guide rails 25 is provided with guide groov...
PUM
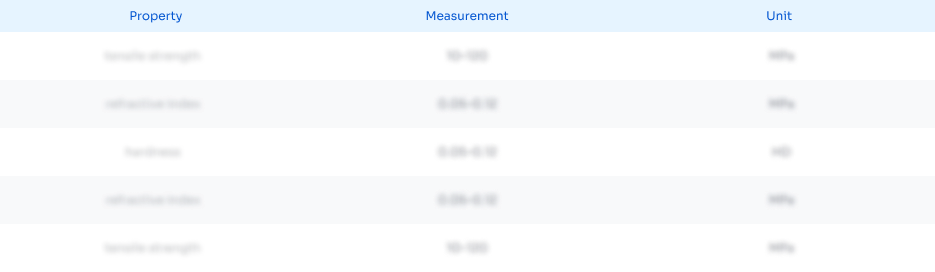
Abstract
Description
Claims
Application Information

- R&D
- Intellectual Property
- Life Sciences
- Materials
- Tech Scout
- Unparalleled Data Quality
- Higher Quality Content
- 60% Fewer Hallucinations
Browse by: Latest US Patents, China's latest patents, Technical Efficacy Thesaurus, Application Domain, Technology Topic, Popular Technical Reports.
© 2025 PatSnap. All rights reserved.Legal|Privacy policy|Modern Slavery Act Transparency Statement|Sitemap|About US| Contact US: help@patsnap.com