Unstacking method for brake discs through robot 3D visualization
A brake disc and robot technology, applied in the field of robots, can solve the problems of poor material rack manufacturing accuracy, brake disk pickup, and low material rack manufacturing accuracy, and achieve the effect of saving space and improving flexibility
- Summary
- Abstract
- Description
- Claims
- Application Information
AI Technical Summary
Problems solved by technology
Method used
Image
Examples
Embodiment approach
[0042] In further embodiments of the present invention, please continue to refer to figure 1 As shown, a 3D camera kit 2 is shown, and the 3D camera kit 2 includes a CCD camera and a laser generator.
[0043] In a further embodiment of the present invention, the laser emitter emits two laser beams, and the position of the brake disc in the vertical direction is detected by the two laser beams.
[0044] In a further embodiment of the present invention, the CCD camera can be used alone as a 2D vision system, and the position of the brake disc on the horizontal plane is detected by the CCD camera.
[0045] In a further embodiment of the present invention, the 3D camera kit 2 is electrically connected to the controller of the robot, and the 3D camera kit is arranged at the end of the gripper 3 .
PUM
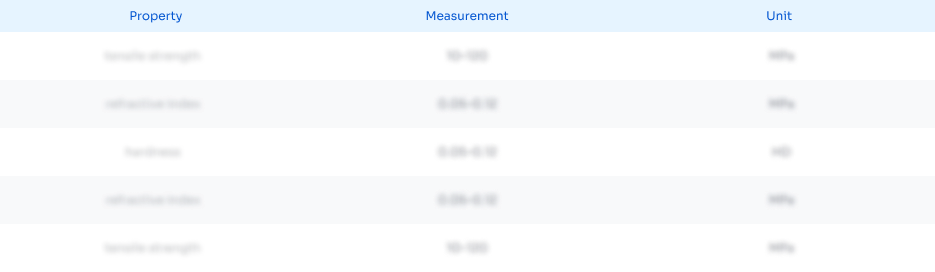
Abstract
Description
Claims
Application Information

- R&D Engineer
- R&D Manager
- IP Professional
- Industry Leading Data Capabilities
- Powerful AI technology
- Patent DNA Extraction
Browse by: Latest US Patents, China's latest patents, Technical Efficacy Thesaurus, Application Domain, Technology Topic, Popular Technical Reports.
© 2024 PatSnap. All rights reserved.Legal|Privacy policy|Modern Slavery Act Transparency Statement|Sitemap|About US| Contact US: help@patsnap.com