Sand mold for casting rotary structure casting and its manufacturing method
A technology of gyratory and casting molds, which is applied in the direction of casting molding equipment, casting molds, and casting mold components. The effect of uniform thickness and reduced skill requirements
- Summary
- Abstract
- Description
- Claims
- Application Information
AI Technical Summary
Problems solved by technology
Method used
Image
Examples
Embodiment Construction
[0026] Embodiments of the present invention will be described in detail below in conjunction with the accompanying drawings.
[0027] Such as Figures 1 to 4B As shown, one embodiment of the present invention provides a sand mold 10 for casting a rotary structure casting, comprising: a first mold unit 12 and a second mold unit 14 that cooperate with each other to form a mold cavity for casting , wherein, the inner surface of the first mold unit 12 is integrally formed with a sand core 16 by 3D printing, and the sand core 16 includes a molding part 18 for forming a casting and a connecting part 20 connecting the molding part 18 with the first mold unit 12 , the inner surface of the second molding unit 14 is provided with a core base 22 that cooperates with the connecting portion 20 .
[0028] It should be noted that the connecting part 20 is used to connect the forming part 18 with the first casting unit 12 means that the connecting part 20 can connect the forming part 18 to t...
PUM
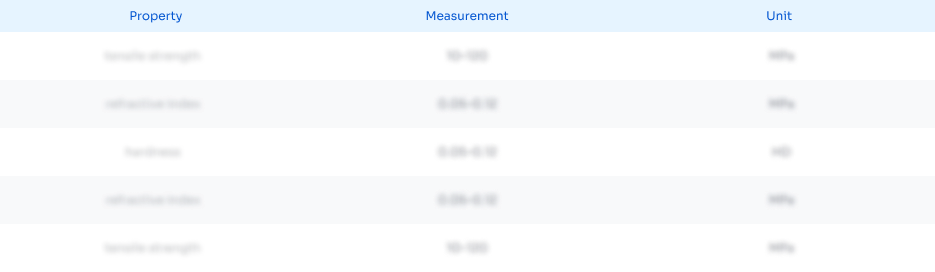
Abstract
Description
Claims
Application Information

- R&D Engineer
- R&D Manager
- IP Professional
- Industry Leading Data Capabilities
- Powerful AI technology
- Patent DNA Extraction
Browse by: Latest US Patents, China's latest patents, Technical Efficacy Thesaurus, Application Domain, Technology Topic, Popular Technical Reports.
© 2024 PatSnap. All rights reserved.Legal|Privacy policy|Modern Slavery Act Transparency Statement|Sitemap|About US| Contact US: help@patsnap.com