A Gravity Driven Caliper Disc Brake
A disc brake and gravity-driven technology, applied in the direction of brake type, axial brake, brake actuator, etc., can solve the problems of complex structure of the brake, no longer usable, reduced braking performance, etc., and achieve uniform force , reduce the impact, reduce the impact of the impact
- Summary
- Abstract
- Description
- Claims
- Application Information
AI Technical Summary
Problems solved by technology
Method used
Image
Examples
Embodiment Construction
[0026] The present invention will be further described in detail below in conjunction with the accompanying drawings and specific embodiments, but the present invention is not limited to these embodiments.
[0027] Such as Figure 1 to Figure 4 As shown, a gravity-driven caliper structure disc brake includes a braking system and a driving system. The braking system includes a caliper brake mechanism for clamping the brake disc 13 and a caliper brake mechanism for touching the brake disc 13. There are four brake arms for the action of the mechanism, and the four brake arms are opposite to each other. They are respectively the right front brake arm 10, the right rear brake arm 11, the left front brake arm 8 and the left rear brake arm. arm 9, the brake system also includes a right transmission shaft 6 and a left transmission shaft 7, the upper part of the right front brake arm 10 and the upper part of the right rear brake arm 11 are sleeved on the right transmission shaft 6, the...
PUM
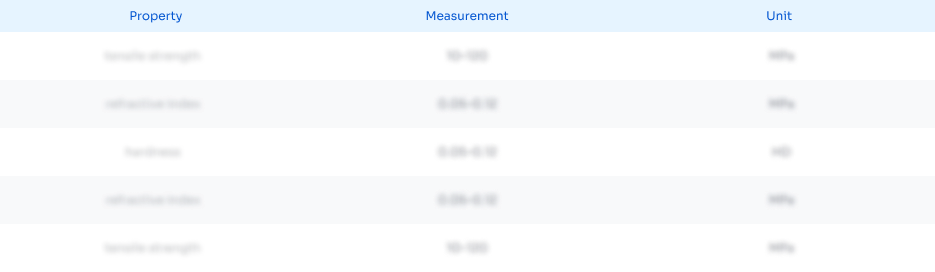
Abstract
Description
Claims
Application Information

- Generate Ideas
- Intellectual Property
- Life Sciences
- Materials
- Tech Scout
- Unparalleled Data Quality
- Higher Quality Content
- 60% Fewer Hallucinations
Browse by: Latest US Patents, China's latest patents, Technical Efficacy Thesaurus, Application Domain, Technology Topic, Popular Technical Reports.
© 2025 PatSnap. All rights reserved.Legal|Privacy policy|Modern Slavery Act Transparency Statement|Sitemap|About US| Contact US: help@patsnap.com