A composite material flexible part assembling deviation analysis method
A technology of composite materials and flexible parts, applied in special data processing applications, instruments, electrical digital data processing, etc.
- Summary
- Abstract
- Description
- Claims
- Application Information
AI Technical Summary
Problems solved by technology
Method used
Image
Examples
Embodiment Construction
[0041] The present invention will be further described below in conjunction with the accompanying drawings and specific embodiments.
[0042] like Figure 8 shown.
[0043] A method for analyzing assembly deviation of composite material flexible parts, which includes the following steps:
[0044] (1) Collect data to obtain the initial manufacturing deviation of composite flexible parts A and B and alpha 1 、α 2 、α 3 ,...,α n , β 1 , β 2 , β 3 ,...,β m ;in Respectively represent the manufacturing deviation of parts A and B passing through the constraint positioning point; represent the manufacturing deviation at the assembly connection points of composite flexible parts A and B respectively; α 1 ~α n and beta 1 ~β m Indicates the actual laying angle error of each layer of composite flexible parts A and B, that is, the difference from the nominal angle, where the subscripts m and n represent the number of layers of composite flexible parts A and B respectively; ...
PUM
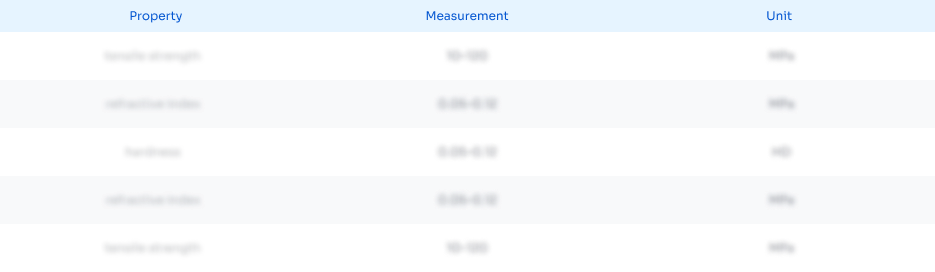
Abstract
Description
Claims
Application Information

- R&D
- Intellectual Property
- Life Sciences
- Materials
- Tech Scout
- Unparalleled Data Quality
- Higher Quality Content
- 60% Fewer Hallucinations
Browse by: Latest US Patents, China's latest patents, Technical Efficacy Thesaurus, Application Domain, Technology Topic, Popular Technical Reports.
© 2025 PatSnap. All rights reserved.Legal|Privacy policy|Modern Slavery Act Transparency Statement|Sitemap|About US| Contact US: help@patsnap.com