Electric water heater
A technology for electric water heaters and heaters, which is applied to water heaters, fluid heaters, lighting and heating equipment, etc., which can solve problems such as inability to disassemble, lower thermal insulation performance, and little difference in water temperature, so as to improve production efficiency and improve Hardening speed, effect of precise control
- Summary
- Abstract
- Description
- Claims
- Application Information
AI Technical Summary
Problems solved by technology
Method used
Image
Examples
Example Embodiment
[0032] Example 1
[0033] Prepare 3 parts by weight of polyether 3050, 10 parts of polyether 4110, 8 parts of polyether 2043, 0.3 parts of methyl chlorophenyl silicone oil, 5 parts of water, 2 parts of calcium bentonite, 4 parts of sepiolite fiber, cross-linked 0.1 part of the foaming catalyst, 1.5 parts of the foaming catalyst and 4 parts of the flame retardant red phosphorus. The foaming catalyst is made of copper isooctanoate, 4-pyrimidine formate, and dimethylethanolamine in a mass ratio of 1:2:6; BDO is selected as the linking agent; the above-mentioned raw materials are mixed uniformly to form a polyether composition, then mixed with 0.8 part of diphenylmethane diisocyanate, and then poured into the cavity of the water heater tank for foaming, and cured at high temperature to obtain the present invention Insulation layer of the water heater used.
Example Embodiment
[0034] Example 2
[0035] Prepare 5 parts by weight of polyether 3050, 15 parts of polyether 4110, 15 parts of polyether 2043, 0.5 parts of methyl chlorophenyl silicone oil, 8 parts of water, 5 parts of calcium bentonite, 6 parts of sepiolite fiber, cross-linked 0.2 parts of foaming catalyst, 1.8 parts of foaming catalyst and 6 parts of flame retardant magnesium hydroxide. The foaming catalyst is made of copper isooctanoate, 4-pyrimidine formate and dimethylethanolamine in a mass ratio of 2:2:6; The crosslinking agent is EG; firstly mix the above-mentioned raw materials uniformly to form a polyether composition, then mix with 0.8-1.5 parts of diphenylmethane diisocyanate, and then pour it into the cavity of the water heater tank for foaming, and obtain it after high temperature curing The thermal insulation layer of the water heater used in the present invention.
Example Embodiment
[0036] Example 3
[0037] Prepare 4 parts of polyether 3050, 13 parts of polyether 4110, 11 parts of polyether 2043, 0.4 parts of methyl chlorophenyl silicone oil, 6 parts of water, 4 parts of calcium bentonite, 5 parts of sepiolite fiber, cross-linked 0.15 parts of foaming catalyst, 1.6 parts of foaming catalyst and 5 parts of flame retardant red phosphorus. The foaming catalyst is made of copper isooctanoate, 4-pyrimidine formate and dimethylethanolamine in a mass ratio of 3:2:6; The coupling agent is DEG; the above-mentioned raw materials are mixed uniformly to form a polyether composition, and then mixed with 1.2 parts of diphenylmethane diisocyanate, then poured into the cavity of the water heater tank for foaming, and cured at high temperature to obtain the present invention Insulation layer of the water heater used.
PUM
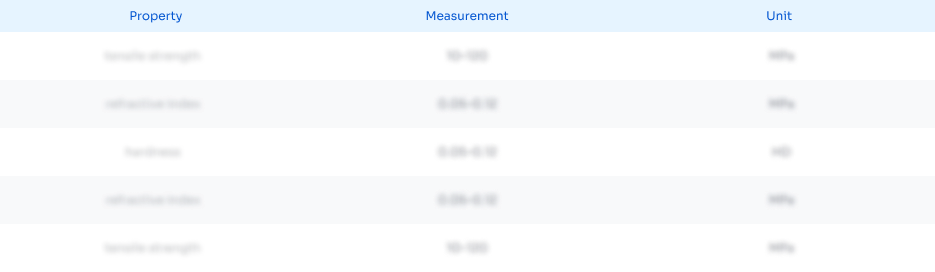
Abstract
Description
Claims
Application Information

- R&D
- Intellectual Property
- Life Sciences
- Materials
- Tech Scout
- Unparalleled Data Quality
- Higher Quality Content
- 60% Fewer Hallucinations
Browse by: Latest US Patents, China's latest patents, Technical Efficacy Thesaurus, Application Domain, Technology Topic, Popular Technical Reports.
© 2025 PatSnap. All rights reserved.Legal|Privacy policy|Modern Slavery Act Transparency Statement|Sitemap|About US| Contact US: help@patsnap.com