Lightweight spray carving mortar
A kind of mortar and lightweight technology, applied in the field of engraving mortar, can solve the problems of loss of realistic effect, inconvenient construction, durability, poor weather resistance, etc., and achieve the effect of stable stacking, convenient modeling, and strong weather resistance
- Summary
- Abstract
- Description
- Claims
- Application Information
AI Technical Summary
Problems solved by technology
Method used
Examples
Embodiment 1
[0022] It is prepared from the following components by mass: 20 parts of inorganic gelling material, 3 parts of redispersible latex powder, 1.5 parts of cellulose ether, 1.5 parts of PP fiber, 48 parts of quartz sand, and 20 parts of heavy calcium powder , 10 parts of light filler, 1.5 parts of anti-shrinkage agent, 0 parts of pigment.
[0023] Portland cement is used as the inorganic cementitious material. The strength grade of Portland cement is 52.5. The redispersible latex powder adopts ethylene-vinyl acetate copolymer. The cellulose ether adopts HPMC material with a viscosity of 40,000. The specification of quartz sand is 60-80 mesh. The lightweight filler adopts vitrified microbeads of 60-120 mesh.
[0024] Prepared by the above-mentioned preparation process, and engraved after mechanical spraying.
Embodiment 2
[0026] It is prepared from the following components by mass: 30 parts of inorganic gelling material, 3 parts of redispersible latex powder, 1.5 parts of cellulose ether, 1.5 parts of PP fiber, 37 parts of quartz sand, and 15 parts of heavy calcium powder , 10 parts of light filler, 1.5 parts of anti-shrinkage agent, 0 parts of pigment.
[0027] The inorganic cementitious material is mixed with Portland cement and slaked lime, and the mass ratio of Portland cement and slaked lime is 1:1. The strength grade of Portland cement is 52.5. Calcium hydroxide in slaked lime is more than 98%. The redispersible latex powder adopts ethylene-vinyl acetate copolymer. The cellulose ether adopts HPMC material with a viscosity of 100,000. The specification of quartz sand is 30-60 mesh. The lightweight filler is mixed with vitrified microbeads and 40-80 mesh vermiculite, and the mass-number ratio of vitrified microbeads and 40-80 mesh vermiculite is 1:1.
[0028] Prepared by the above-ment...
Embodiment 3
[0030] It is prepared from the following components by mass: 30 parts of inorganic gelling material, 2 parts of redispersible latex powder, 1 part of cellulose ether, 1.5 parts of PP fiber, 30 parts of quartz sand, and 25 parts of heavy calcium powder , 10 parts of light filler, 1 part of anti-shrinkage agent, 0 parts of pigment.
[0031] The inorganic cementitious material is mixed with Portland cement and slaked lime, and the mass ratio of Portland cement and slaked lime is 2:1. The strength grade of Portland cement is 52.5. Calcium hydroxide in slaked lime is more than 98%. The redispersible latex powder adopts ethylene-vinyl acetate copolymer. The cellulose ether adopts HPMC material with a viscosity of 100,000. The specification of quartz sand is 60-80 mesh. The lightweight filler is mixed with vitrified microbeads and 40-80 mesh vermiculite, and the mass-number ratio of vitrified microbeads and 40-80 mesh vermiculite is 1:1.
[0032] Prepared by the above-mentioned ...
PUM
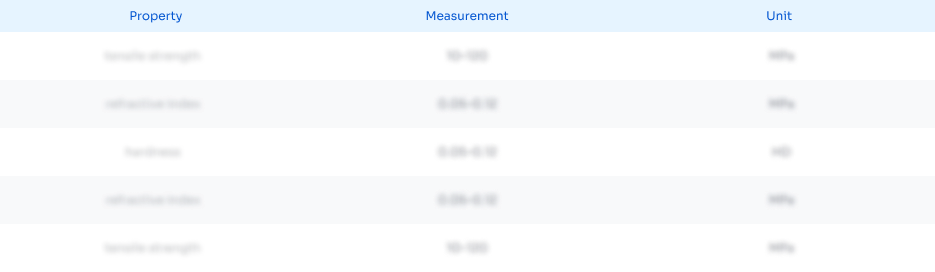
Abstract
Description
Claims
Application Information

- R&D
- Intellectual Property
- Life Sciences
- Materials
- Tech Scout
- Unparalleled Data Quality
- Higher Quality Content
- 60% Fewer Hallucinations
Browse by: Latest US Patents, China's latest patents, Technical Efficacy Thesaurus, Application Domain, Technology Topic, Popular Technical Reports.
© 2025 PatSnap. All rights reserved.Legal|Privacy policy|Modern Slavery Act Transparency Statement|Sitemap|About US| Contact US: help@patsnap.com