Improved Analytical Model of Motor Stator Core Vibration Caused by Magnetostriction
A stator core, motor stator technology, applied in the direction of electrical digital data processing, instrumentation, design optimization/simulation, etc., can solve the problem that the vibration displacement, stress and strain distribution characteristics of the motor stator core yoke cannot be calculated, and the core axis is not considered. Problems such as directional vibration and large computer resources, etc., to achieve accurate and reliable calculation results, fast calculation speed, and small calculation amount
- Summary
- Abstract
- Description
- Claims
- Application Information
AI Technical Summary
Problems solved by technology
Method used
Image
Examples
Embodiment
[0147] The invention uses the finite element method to verify the analytical calculation model of the motor stator core vibration caused by magnetostriction. Taking a 2.1kW radial flux amorphous alloy permanent magnet motor as an example for quantitative analysis, the 2.1kW motor has a rated frequency of 267Hz, 8 poles and 36 slots. The two methods used the same performance parameters during analysis. Use 2D finite element to analyze the electromagnetic field of permanent magnet motor, and establish a quarter-period model of the motor such as Figure 5 Shown. The tangential and radial magnetic flux density at point B of the stator core yoke of the motor is calculated as a function of time. Image 6 As shown, the radial and tangential magnetic flux density at point A of the motor stator core tooth position changes with time. Figure 7 Shown. From Image 6 with 7 It can be seen that the magnetic field of the stator core yoke of the motor is mainly tangential, and the magnetic fi...
PUM
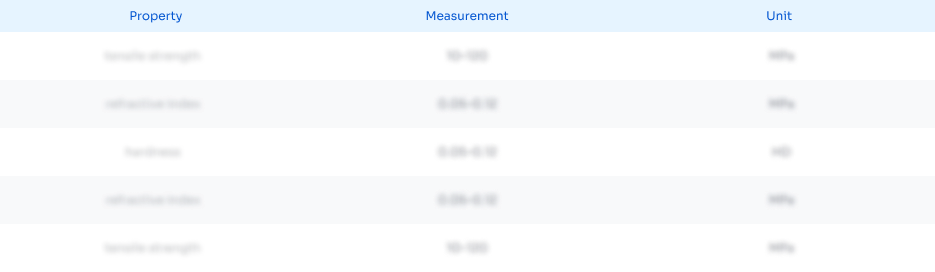
Abstract
Description
Claims
Application Information

- R&D Engineer
- R&D Manager
- IP Professional
- Industry Leading Data Capabilities
- Powerful AI technology
- Patent DNA Extraction
Browse by: Latest US Patents, China's latest patents, Technical Efficacy Thesaurus, Application Domain, Technology Topic, Popular Technical Reports.
© 2024 PatSnap. All rights reserved.Legal|Privacy policy|Modern Slavery Act Transparency Statement|Sitemap|About US| Contact US: help@patsnap.com