Automatic industrial cascaded multi-node control system of non-full-code parallel bus
An industrial automation and control system technology, applied in the field of warehouse intelligent control and logistics management, can solve the problems of high price, many output signals, and large long-distance loss, and achieve high warehouse location size adaptability, small PCB size, and easy wiring Effect
- Summary
- Abstract
- Description
- Claims
- Application Information
AI Technical Summary
Problems solved by technology
Method used
Image
Examples
Embodiment Construction
[0027] like Figure 1-2 As shown, the non-full-code parallel bus cascaded multi-node industrial automation control system disclosed by the present invention includes node circuits distributed at each industrial automation physical location, and each node circuit is sequentially cascaded through the parallel bus, and the upper In the driver program, the machine passes all the node circuit addresses through the non-full code list and numbers them. When the corresponding node circuit needs to work, the non-full code is taken out through the number and output to the parallel bus controller through the output interface of the host computer. The parallel bus The controller converts any form of bus protocol of the computer, such as USB, COM, network, PCI, PXI, PCIe, etc., into a parallel bus, and can also directly PLC to control the parallel bus to drive the corresponding node circuit to work.
[0028] The non-full-code coding principle is introduced below: the non-full-code method i...
PUM
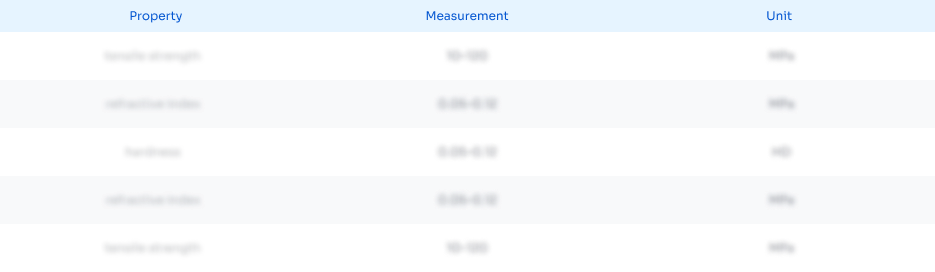
Abstract
Description
Claims
Application Information

- Generate Ideas
- Intellectual Property
- Life Sciences
- Materials
- Tech Scout
- Unparalleled Data Quality
- Higher Quality Content
- 60% Fewer Hallucinations
Browse by: Latest US Patents, China's latest patents, Technical Efficacy Thesaurus, Application Domain, Technology Topic, Popular Technical Reports.
© 2025 PatSnap. All rights reserved.Legal|Privacy policy|Modern Slavery Act Transparency Statement|Sitemap|About US| Contact US: help@patsnap.com