Catalyst composition for waste rubber thermocracking
A catalyst and thermal cracking technology, which is applied in the direction of physical/chemical process catalysts, chemical/physical processes, and preparation of liquid hydrocarbon mixtures, etc. It can solve problems such as little effect on thermal cracking efficiency, poor catalyst stability, and complicated manufacturing processes. Achieve the effects of improving thermal cracking efficiency, good stability, and simple preparation process
- Summary
- Abstract
- Description
- Claims
- Application Information
AI Technical Summary
Problems solved by technology
Method used
Examples
Embodiment 1
[0017] The proportion of ingredients used is: 5 parts of aluminum binder, 10 parts of zirconia, 15 parts of natural minerals, 10 parts of clay, 5 parts of tridecyltrimethylammonium bromide, 8 parts of citric acid and absolute ethanol 10 servings.
[0018] In this embodiment, the natural minerals are a mixture of 30% kaolin, 20% montmorillonite, 10% diatomaceous earth, 10% hydrotalcite, 10% bentonite, and 20% retort clay.
[0019] The preparation method of the present embodiment comprises the following steps:
[0020] A. Mix natural minerals, zirconia, and clay and put them into a pulverizer to pulverize, then add 1 / 3 aluminum binder, stir and mix to form mixture A;
[0021] B. Add tridecyltrimethylammonium bromide and absolute ethanol to mixture A, add the mixture to a water bath for heating, control the temperature of the water bath at 45°C, heat for 45 minutes and then keep the temperature for 30 minutes to obtain mixture B;
[0022] C. Add 2 / 3 of the aluminum binder to th...
Embodiment 2
[0025] The proportion of ingredients used is: 25 parts of aluminum binder, 35 parts of zirconia, 55 parts of natural minerals, 30 parts of clay, 20 parts of tridecyltrimethylammonium bromide, 20 parts of citric acid and absolute ethanol 30 servings.
[0026] In this embodiment, the natural minerals are a mixture of 30% kaolin, 20% montmorillonite, 10% diatomaceous earth, 10% hydrotalcite, 10% bentonite, and 20% retort clay.
[0027] The preparation method of the present embodiment comprises the following steps:
[0028] A. Mix natural minerals, zirconia, and clay and put them into a pulverizer to pulverize, then add 1 / 3 aluminum binder, stir and mix to form mixture A;
[0029] B. Add tridecyltrimethylammonium bromide and absolute ethanol to mixture A, add the mixture to a water bath for heating, control the temperature of the water bath at 65°C, heat for 55 minutes and then keep the temperature for 30 minutes to obtain mixture B;
[0030] C. Add 2 / 3 of the aluminum binder to...
Embodiment 3
[0033] The proportion of ingredients used is: 10 parts of aluminum binder, 15 parts of zirconia, 20 parts of natural minerals, 15 parts of clay, 10 parts of tridecyltrimethylammonium bromide, 10 parts of citric acid and absolute ethanol 13 servings.
[0034] In this embodiment, the natural minerals are a mixture of 30% kaolin, 20% montmorillonite, 10% diatomaceous earth, 10% hydrotalcite, 10% bentonite, and 20% retort clay.
[0035] The preparation method of the present embodiment comprises the following steps:
[0036] A. Mix natural minerals, zirconia, and clay and put them into a pulverizer to pulverize, then add 1 / 3 aluminum binder, stir and mix to form mixture A;
[0037] B. Add tridecyltrimethylammonium bromide and absolute ethanol to mixture A, add the mixture into a water bath for heating, control the temperature of the water bath at 50°C, heat for 48 minutes and then keep the temperature for 30 minutes to obtain mixture B;
[0038] C. Add 2 / 3 of the aluminum binder ...
PUM
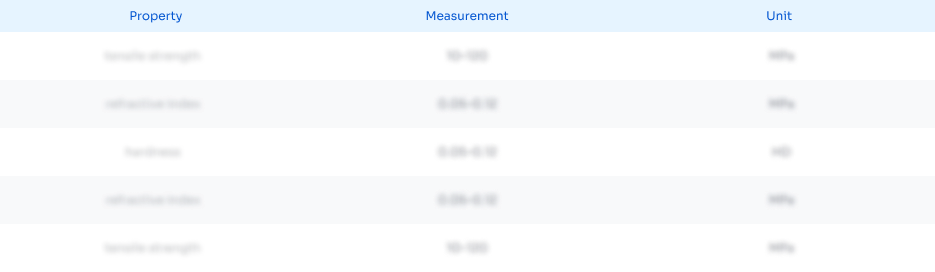
Abstract
Description
Claims
Application Information

- R&D Engineer
- R&D Manager
- IP Professional
- Industry Leading Data Capabilities
- Powerful AI technology
- Patent DNA Extraction
Browse by: Latest US Patents, China's latest patents, Technical Efficacy Thesaurus, Application Domain, Technology Topic, Popular Technical Reports.
© 2024 PatSnap. All rights reserved.Legal|Privacy policy|Modern Slavery Act Transparency Statement|Sitemap|About US| Contact US: help@patsnap.com