Manufacturing process of VARI composite material foam sandwiched wedge-shaped part and obtained wedge-shaped part
A composite material and manufacturing process technology, applied in aircraft parts, weight reduction, transportation and packaging, etc., can solve the problems of poor bonding effect between foam bottom fabric foam and skin, unqualified product quality, dry spots on the product surface, etc. To achieve the effect of solving edge effects, improving product quality and pass rate, and eliminating edge effects
- Summary
- Abstract
- Description
- Claims
- Application Information
AI Technical Summary
Problems solved by technology
Method used
Image
Examples
Embodiment
[0027] A manufacturing process for VARI shaped composite foam sandwich wedges, such as figure 1 As shown, first, a layer of release cloth-6 with air-guiding function is laid on the forming mold 1, and the lower skin 3 fabric is assisted by laser projection, and the lower skin 3 is packaged and pre-compacted in an oven; to be formed The temperature of the mold 1 is lowered to room temperature, the wedge-shaped sandwich foam 4 is placed and positioned, and the first layer of fabric covered with the skin 5 is packaged and pre-compacted in an oven. Leather 5 remaining fabric.
[0028] According to the specification requirements of the vacuum-assisted molding process VARI, lay the release cloth 2 12, the diversion medium 77, the glue injection pipeline 9, and the air extraction pipeline 10 in sequence, and paste the sealant strip 2 at a position 10cm~30cm away from the product laying line 1. Seal the vacuum bag film 8 onto the sealing strip 2 to complete the packaging, send it to ...
PUM
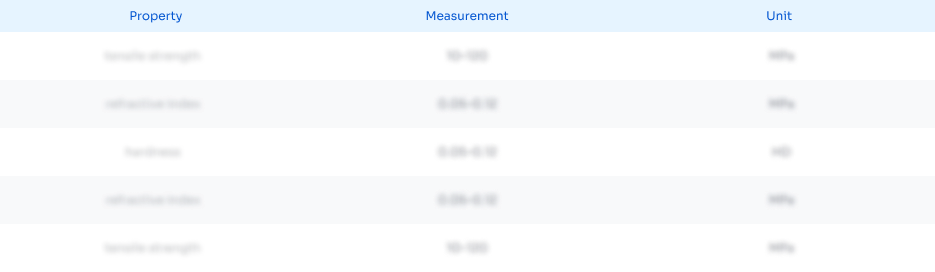
Abstract
Description
Claims
Application Information

- R&D
- Intellectual Property
- Life Sciences
- Materials
- Tech Scout
- Unparalleled Data Quality
- Higher Quality Content
- 60% Fewer Hallucinations
Browse by: Latest US Patents, China's latest patents, Technical Efficacy Thesaurus, Application Domain, Technology Topic, Popular Technical Reports.
© 2025 PatSnap. All rights reserved.Legal|Privacy policy|Modern Slavery Act Transparency Statement|Sitemap|About US| Contact US: help@patsnap.com