A method for preparing high-nitrogen vanadium nitride with coke
A technology for nitriding vanadium and coke, applied in the field of vanadium alloy, can solve the problem that high nitrogen vanadium nitride technology is rare, and achieve the effect of stable and uniform circulation
- Summary
- Abstract
- Description
- Claims
- Application Information
AI Technical Summary
Problems solved by technology
Method used
Image
Examples
Embodiment 1
[0060] This embodiment provides a kind of production method that substitutes 5wt% graphite with coke to prepare vanadium nitride, the ash content in the coke is 12~13.5wt%, the content of silicon dioxide in the ash is ≥55wt%, and the content of iron in the ash is 1wt%;
[0061] The method comprises the steps of:
[0062] Put 1000kg of vanadium trioxide, 247kg of graphite, 13kg of coke and 99.2kg of water into the mixer and press the balls. Control the flow of nitrogen gas flow to 200m 3 / h, the temperature of the carbon reduction section is 800°C, the central temperature of the nitriding section is 1450°C, the upper temperature of the cooling section is 900°C, the lower temperature of the cooling section is ≤150°C, and the residence time of raw materials in the nitriding section is After 20 hours, the vanadium nitride product was obtained.
Embodiment 2
[0066] This embodiment provides a kind of production method that substitutes 10wt% graphite with coke to prepare vanadium nitride, the ash content in the coke is 12~13.5wt%, the content of silicon dioxide in the ash is ≥ 55wt%, and the content of iron in the ash is 1wt%;
[0067] The method comprises the steps of:
[0068] Put 1000kg of vanadium trioxide, 234kg of graphite, 26kg of coke and 99.2kg of water into the mixer and press the balls. Control the flow of nitrogen gas flow to 200m 3 / h, the temperature of the carbon reduction section is 800°C, the central temperature of the nitriding section is 1450°C, the temperature of the upper part of the cooling section is 800°C, the temperature of the lower part of the cooling section is ≤150°C, and the residence time of raw materials in the nitriding section is 16h, the vanadium nitride product was obtained.
Embodiment 3
[0072] This embodiment provides a kind of production method that substitutes 15wt% graphite with coke to prepare vanadium nitride, the ash content in the coke is 12~13.5wt%, the content of silicon dioxide in the ash is ≥ 55wt%, and the content of iron in the ash is 1wt%;
[0073] The method comprises the steps of:
[0074] Put 1000kg of vanadium trioxide, 221kg of graphite, 39kg of coke and 99.2kg of water into the mixer and press the balls. After drying and screening, the raw pellets are put into the pusher kiln for firing. During the firing process Control the flow rate of nitrogen gas flow to 350m 3 / h, the temperature of the carbon reduction section is 1100°C, the central temperature of the nitriding section is 1500°C, the temperature of the upper part of the cooling section is 900°C, the temperature of the lower part of the cooling section is ≤150°C, and the residence time of raw materials in the nitriding section is After 20 hours, the vanadium nitride product was obta...
PUM
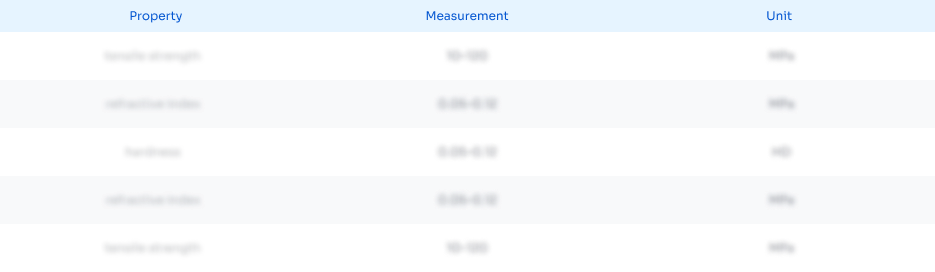
Abstract
Description
Claims
Application Information

- R&D Engineer
- R&D Manager
- IP Professional
- Industry Leading Data Capabilities
- Powerful AI technology
- Patent DNA Extraction
Browse by: Latest US Patents, China's latest patents, Technical Efficacy Thesaurus, Application Domain, Technology Topic, Popular Technical Reports.
© 2024 PatSnap. All rights reserved.Legal|Privacy policy|Modern Slavery Act Transparency Statement|Sitemap|About US| Contact US: help@patsnap.com