Controllable composite damping structure adopting magnetostrictive material
A magnetostrictive material and composite damping technology, applied in the direction of vibrating fluids, electromechanical devices, electrical components, etc., can solve the problems of large control circuit volume, poor energy conversion characteristics, high impedance, etc., and achieve small volume, volume change The effect of small and large control range
- Summary
- Abstract
- Description
- Claims
- Application Information
AI Technical Summary
Problems solved by technology
Method used
Image
Examples
Embodiment 1
[0026] to combine figure 1 , this embodiment includes: a viscoelastic material layer 1, a magnetostrictive material layer 2, an elastic substrate 3, an electromagnetic induction coil 4, a magnetic conductor 5, a permanent magnet 6 and a matching control circuit 7; the viscoelastic material layer 1 is compounded in The magnetostrictive material layer 2 provides initial damping for the composite damping structure; the magnetostrictive material layer 2 is compounded on the elastic substrate 3 for coupling the mechanical deformation of the elastic substrate 3, and based on its inverse magnetostrictive effect, the The mechanical energy generated by the mechanical deformation of the elastic base layer 3 is converted into magnetic energy, thereby generating dynamic magnetization; the electromagnetic induction coil 4 is used to convert the dynamic magnetization into electrical energy and output an electrical signal, and then realize damping control under the action of the matching cont...
Embodiment 2
[0030] to combine image 3 , the composite damping structure shown in this embodiment is basically the same as that of Embodiment 1, the difference is that this embodiment does not use a magnetic conductor, but the electromagnetic induction coil 4 is directly wound on the viscoelastic material layer 1, the magnetic induction coil The composite body formed by the elastic material layer 2 and the elastic substrate 3 realizes electromagnetic induction and converts magnetic energy into electrical energy. At the same time, by arranging the permanent magnet 6 at one end of the magnetostrictive material, the application of the bias magnetic field can be realized without providing a magnetizer.
[0031]In fact, in the present invention, the permanent magnet 6 can be flexibly arranged in different positions according to the use environment, as long as a bias magnetic field can be applied to the magnetostrictive material layer 2, so that the magnetostrictive material 2 works at the maxi...
PUM
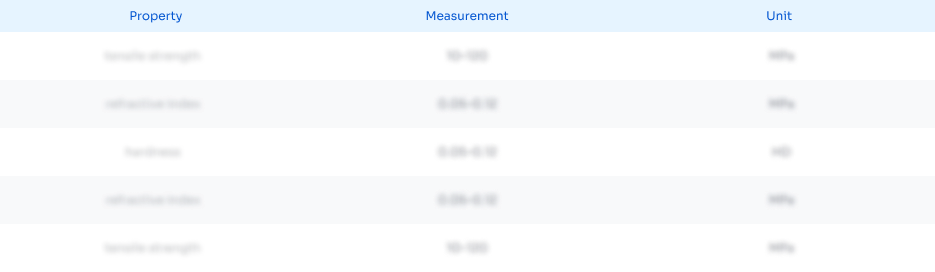
Abstract
Description
Claims
Application Information

- R&D
- Intellectual Property
- Life Sciences
- Materials
- Tech Scout
- Unparalleled Data Quality
- Higher Quality Content
- 60% Fewer Hallucinations
Browse by: Latest US Patents, China's latest patents, Technical Efficacy Thesaurus, Application Domain, Technology Topic, Popular Technical Reports.
© 2025 PatSnap. All rights reserved.Legal|Privacy policy|Modern Slavery Act Transparency Statement|Sitemap|About US| Contact US: help@patsnap.com