Thermal isolation and sealing electromagnet assembly
A technology for sealing electromagnets and electromagnets, applied in electrical components, transformer/inductor cores, transformer/inductor components, etc. Guaranteed effect of reliability
- Summary
- Abstract
- Description
- Claims
- Application Information
AI Technical Summary
Problems solved by technology
Method used
Image
Examples
Embodiment Construction
[0018] refer to figure 1 . In the embodiment described below, a heat-insulated and sealed electromagnet assembly mainly includes an electromagnet housing 1 with a multi-stage diameter and a concentric cavity cavity with a multi-stage diameter, which is concentrically assembled in the electromagnet case The outside of the body 1 acts as a fastening nut 2 for fixing the electromagnet, and the iron core 5 and the electromagnet spring 11 assembled in the central cavity of the electromagnet housing 1 are axially positioned at the port of the cavity of the inner frame 12 and the armature. The inner frame 12 between the 3, the coil 4 covered by the coil frame 6 is assembled in the groove of the iron core 5 opening downwards, respectively connected to the two connecting rods 10 at both ends of the wire of the coil 4, and the upper end surface of the iron core 5 is tight. Attached to the lower end surface of the inner frame 12, the cylindrical scapular surface formed on the upper par...
PUM
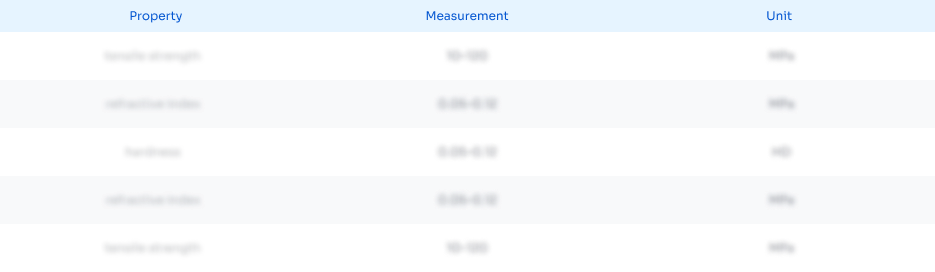
Abstract
Description
Claims
Application Information

- Generate Ideas
- Intellectual Property
- Life Sciences
- Materials
- Tech Scout
- Unparalleled Data Quality
- Higher Quality Content
- 60% Fewer Hallucinations
Browse by: Latest US Patents, China's latest patents, Technical Efficacy Thesaurus, Application Domain, Technology Topic, Popular Technical Reports.
© 2025 PatSnap. All rights reserved.Legal|Privacy policy|Modern Slavery Act Transparency Statement|Sitemap|About US| Contact US: help@patsnap.com