Cable sheath for high strength building and preparation method of cable sheath
A technology for cable sheathing and construction, which is applied in the field of high-strength construction cable sheathing and its preparation. It can solve the problems of endangering life and property safety, unreasonable ingredients and general insulation performance, etc., and achieves easy operation and aging resistance. Excellent, short burning distance effect
- Summary
- Abstract
- Description
- Claims
- Application Information
AI Technical Summary
Problems solved by technology
Method used
Examples
preparation example Construction
[0021] A preparation method for a high-strength construction cable sheath, comprising the steps of:
[0022] S1. Weigh a certain amount of 22-35 parts of polyvinyl fluoride resin, 15-25 parts of modified epoxy resin, 16-22 parts of methyl pentachlorostearate, 10-15 parts of hydrotalcite, and 15-22 parts of expanded graphite 10-20 parts of nitrile rubber, 11-15 parts of ethylene bis stearamide, 33-36 parts of chlorinated paraffin, 10-20 parts of carbon fiber, 3-9 parts of calcium stearate, 6-10 parts of accelerator The raw materials are added to a high-efficiency mixing mixer and fully mixed and stirred for 5-10 minutes to obtain a mixture;
[0023] S2. Add the mixture obtained in step S1 into a torque rheometer, and melt at a temperature of 150-250° C. for 5-10 minutes;
[0024] S3. Add 2-6 parts of antioxidant, 5-8 parts of flame retardant and 2-6 parts of plasticizer to the mixture obtained in step S2, first react at a temperature of 60-80°C for 15-20min, and then use 500- ...
Embodiment 1
[0026] S1. Weigh a certain amount of 22 parts of polyvinyl fluoride resin, 15 parts of modified epoxy resin, 16 parts of methyl pentachlorostearate, 10 parts of hydrotalcite, 15 parts of expanded graphite, 10 parts of nitrile rubber, ethylene Add 11 parts of bis-stearamide, 33 parts of chlorinated paraffin, 10 parts of carbon fiber, 3 parts of calcium stearate, and 6 parts of accelerator into a high-efficiency mixing mixer and fully mix and stir for 5 minutes to obtain a mixture;
[0027] S2. Add the mixture obtained in step S1 into a torque rheometer, and melt at a temperature of 150-250° C. for 5-10 minutes;
[0028] S3. Add 2-6 parts of antioxidant, 5-8 parts of flame retardant and 2-6 parts of plasticizer to the mixture obtained in step S2, first react at a temperature of 60-80°C for 15-20min, and then use 500- Stir quickly at a rate of 800r / min for 20-30min, then pour into a single-screw granulator for granulation; after cooling, the cable sheath is obtained.
Embodiment 2
[0030] S1. Weigh a certain amount of 27 parts of polyvinyl fluoride resin, 22 parts of modified epoxy resin, 18 parts of methyl pentachlorostearate, 12 parts of hydrotalcite, 18 parts of expanded graphite, 15 parts of nitrile rubber, ethylene Add 13 parts of bis-stearamide, 34 parts of chlorinated paraffin, 16 parts of carbon fiber, 5 parts of calcium stearate, and 7 parts of accelerator into a high-efficiency mixing mixer and fully mix and stir for 5-10 minutes to obtain a mixture;
[0031] S2. Add the mixture obtained in step S1 into a torque rheometer, and melt at a temperature of 150-250° C. for 5-10 minutes;
[0032] S3. Add 2-6 parts of antioxidant, 5-8 parts of flame retardant and 2-6 parts of plasticizer to the mixture obtained in step S2, first react at a temperature of 60-80°C for 15-20min, and then use 500- Stir quickly at a rate of 800r / min for 20-30min, then pour into a single-screw granulator for granulation; after cooling, the cable sheath is obtained.
PUM
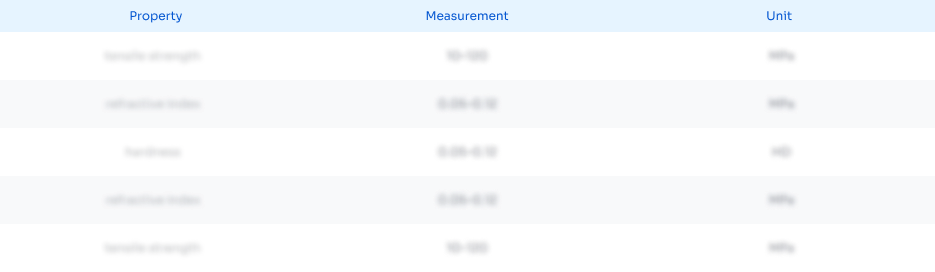
Abstract
Description
Claims
Application Information

- Generate Ideas
- Intellectual Property
- Life Sciences
- Materials
- Tech Scout
- Unparalleled Data Quality
- Higher Quality Content
- 60% Fewer Hallucinations
Browse by: Latest US Patents, China's latest patents, Technical Efficacy Thesaurus, Application Domain, Technology Topic, Popular Technical Reports.
© 2025 PatSnap. All rights reserved.Legal|Privacy policy|Modern Slavery Act Transparency Statement|Sitemap|About US| Contact US: help@patsnap.com