Continuous cast-welding device for busbar and polar column of lead-acid battery
A lead-acid battery and busbar technology, applied in battery pack parts, circuits, electrical components, etc., can solve problems such as increasing the space occupied by production equipment, unsmooth production, and long production cycle, and achieve high automation, The effect of shortening cycle time and improving production efficiency
- Summary
- Abstract
- Description
- Claims
- Application Information
AI Technical Summary
Problems solved by technology
Method used
Image
Examples
Embodiment 1
[0027] as attached figure 1 As shown, the combination of each independent equipment of the lead-acid battery casting and welding equipment of the present invention and the transmission flow of the mold and the fixture. Use multiple molds and fixtures to independently implement each action of the casting and welding process on each equipment, and automatically transfer the molds and fixtures between each equipment.
[0028] The operator only needs to put the jig equipped with the pole group on the automatic conveying raceway at the casting and welding preparation station. The automatic mechanical device lifts it up and positions it for standby; the lead alloy liquid temperature of the lead-melting furnace is used to raise the temperature of the mold suitable for casting welding temperature, and it is lifted out of the lead-melting furnace by another conveying device and positioned precisely; Insert into the engraved grooves of the bus bar and the pole of the mold to complete t...
Embodiment 2
[0037] The battery is designed as 6 single-cell 12V electric bicycle battery pole groups of the type 6DZM10, and loaded into a special pole group fixture. After aligning each pole group tab and pressing the pole group tightly, put the fixture into On the transmission raceway of the cast welding equipment made according to the technical process of the present invention. The equipment firstly automatically brushes off the oxide attached to the surface of the lug and automatically brushes the casting flux to complete the preparation for casting and welding.
[0038] The completion time of each process in the first production cycle after the equipment is started is as follows:
[0039] Casting and welding mold heating: 30 seconds;
[0040] Cast welding: 7 seconds;
[0041] Mold and busbar cooling after casting: 24 seconds;
[0042] Demoulding between the busbar and the casting and welding mold: 6 seconds;
[0043] The insertion of the electrode group into the battery case slot...
PUM
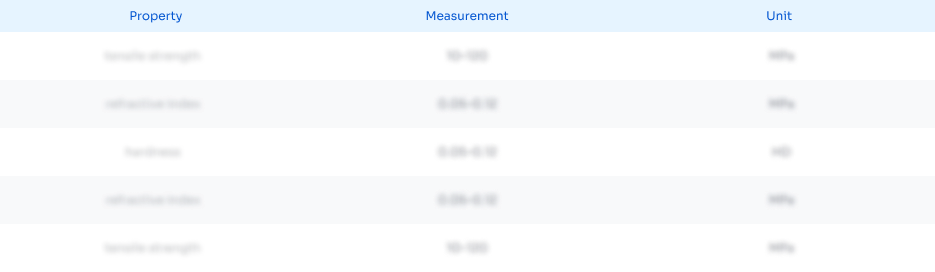
Abstract
Description
Claims
Application Information

- R&D
- Intellectual Property
- Life Sciences
- Materials
- Tech Scout
- Unparalleled Data Quality
- Higher Quality Content
- 60% Fewer Hallucinations
Browse by: Latest US Patents, China's latest patents, Technical Efficacy Thesaurus, Application Domain, Technology Topic, Popular Technical Reports.
© 2025 PatSnap. All rights reserved.Legal|Privacy policy|Modern Slavery Act Transparency Statement|Sitemap|About US| Contact US: help@patsnap.com