Automatic butt joint charging system and automatic butt joint charging method for robot
An automatic docking and charging system technology, applied in battery circuit devices, data exchange chargers, control/regulation systems, etc., can solve problems such as trouble, inconvenience, and inability to charge robots, reduce manual operations, realize automatic docking, Achieve the effect of automatic charging
- Summary
- Abstract
- Description
- Claims
- Application Information
AI Technical Summary
Problems solved by technology
Method used
Image
Examples
Embodiment 1
[0037] Embodiment 1. A robot automatic docking and charging system.
[0038] see figure 1 and figure 2 The robot automatic docking and charging system provided in this embodiment is used to automatically dock and charge the robot, including a robot and a charging pile. Two receiving infrared sensors 4 and robot control terminals, the charging pile includes a charging pile housing 13, a positive contact copper plate 5 of the charging pile, a charging insulating sleeve 6, a negative contact copper plate 7 of the charging pile, a guide sleeve 8, (2n+1) An infrared emission sensor 9, a baffle 10, a limit switch 11, a charging adapter 12 and a charging pile control terminal.
[0039] The positive contact copper plate 1 of the robot and the negative contact copper plate 3 of the robot are closely fitted and installed on the insulating sleeve 2, the insulating sleeve 2 is installed on the rear shell of the robot, and the two receiving infrared sensors 4 are installed on the adjust...
Embodiment 2
[0044] Embodiment 2. A method for automatic docking and charging of a robot.
[0045] see image 3 In this embodiment, the method for realizing automatic docking and charging by using the robot automatic docking and charging system in the above-mentioned embodiment 1 includes:
[0046] (2n+1) transmitting infrared sensors on the charging pile transmit infrared signals to the robot, where n≥1, and n is a positive integer; two receiving infrared sensors on the robot are used to receive the emitted infrared signals respectively , and send the strength of the received infrared signal to the robot control terminal; the robot control terminal judges the deviation position of the robot car body according to the intensity of the infrared signals received by the two receiving infrared sensors, and drives the motor driver on the robot to drive the corresponding The motor adjusts the moving position of the robot body until the intensity of the infrared signals received by the two receiv...
PUM
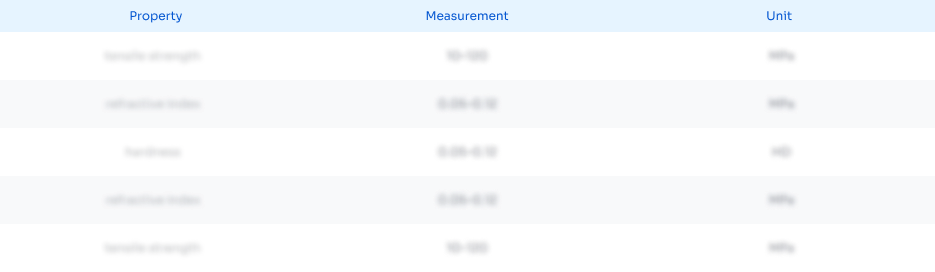
Abstract
Description
Claims
Application Information

- R&D
- Intellectual Property
- Life Sciences
- Materials
- Tech Scout
- Unparalleled Data Quality
- Higher Quality Content
- 60% Fewer Hallucinations
Browse by: Latest US Patents, China's latest patents, Technical Efficacy Thesaurus, Application Domain, Technology Topic, Popular Technical Reports.
© 2025 PatSnap. All rights reserved.Legal|Privacy policy|Modern Slavery Act Transparency Statement|Sitemap|About US| Contact US: help@patsnap.com