Multi-pipe discharge device of sinter shaft kiln waste heat recovery system
A waste heat recovery system and technology for sintering ore, applied in furnace control devices, processing discharged materials, vertical furnaces, etc., can solve the problems of insufficient cooling, fast feeding, and red material discharge, so as to prevent red material accidents. Effect
- Summary
- Abstract
- Description
- Claims
- Application Information
AI Technical Summary
Problems solved by technology
Method used
Image
Examples
Embodiment Construction
[0013] The present invention will be further described in detail below in conjunction with the accompanying drawings and embodiments.
[0014] see figure 1 , as shown in 2, a multi-tube discharge device of a sinter shaft kiln waste heat recovery system in this embodiment includes a central air inlet pipe 2 arranged at the bottom of the cooling section of the kiln body 1, and the central air inlet pipe 2 There are multiple peripheral air inlet pipes 3 evenly arranged on both sides of the kiln body. The peripheral air inlet pipes 3 are arranged in a radial or "well" shape at the bottom of the kiln body. Each peripheral air inlet pipe 3 is independently adjusted according to the discharge temperature to reach the kiln body. The sinter temperature, air temperature, and airflow distribution on the same section tend to be consistent, and the sinter on the same section is also in a balanced state of feeding. The central air inlet pipe 2 and a plurality of peripheral air inlet pipes ...
PUM
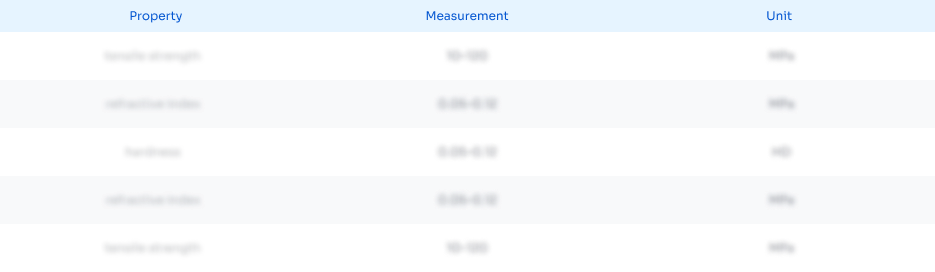
Abstract
Description
Claims
Application Information

- R&D
- Intellectual Property
- Life Sciences
- Materials
- Tech Scout
- Unparalleled Data Quality
- Higher Quality Content
- 60% Fewer Hallucinations
Browse by: Latest US Patents, China's latest patents, Technical Efficacy Thesaurus, Application Domain, Technology Topic, Popular Technical Reports.
© 2025 PatSnap. All rights reserved.Legal|Privacy policy|Modern Slavery Act Transparency Statement|Sitemap|About US| Contact US: help@patsnap.com