An Adaptive Pipeline Flaw Detection Robot
A robot and self-adaptive technology, applied in the direction of pipe components, special pipes, mechanical equipment, etc., can solve the problems that accidental and randomness cannot completely eliminate hidden dangers of pipelines, and achieve the effects of saving resources, reducing wear and avoiding accidental risks
- Summary
- Abstract
- Description
- Claims
- Application Information
AI Technical Summary
Problems solved by technology
Method used
Image
Examples
Embodiment Construction
[0028] The present invention will be described in further detail below in conjunction with specific embodiments.
[0029] like Figure 1 to Figure 7 As shown, an adaptive pipeline flaw detection robot includes bionic torpedo probes symmetrically arranged at both ends of the flaw detection robot, respectively connected to two power transmission devices 2 at the rear ends of the bidirectional bionic torpedo probes, The shaft device 13 is connected to the power transmission device 3 between the two power transmission devices 2, and the power transmission device 2 includes a fixed frame connected and fixed on the rear end of the bidirectional bionic torpedo probe, uniform along the circumferential direction of the fixed frame. At least three driving wheel mechanisms are distributed, and the fixed frame is also provided with a wheel mechanism radial adjustment device for respectively adjusting the radial position of each driving wheel mechanism; the power transmission device 3 incl...
PUM
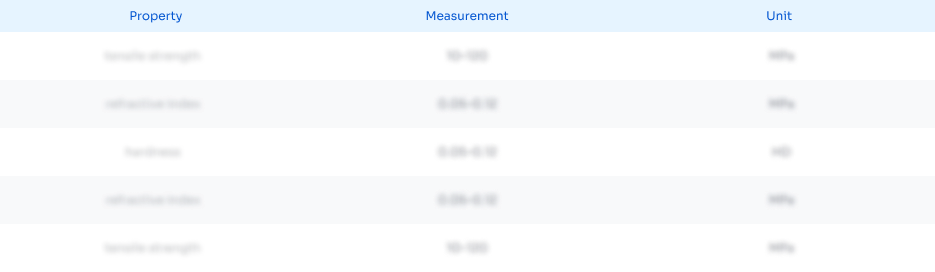
Abstract
Description
Claims
Application Information

- Generate Ideas
- Intellectual Property
- Life Sciences
- Materials
- Tech Scout
- Unparalleled Data Quality
- Higher Quality Content
- 60% Fewer Hallucinations
Browse by: Latest US Patents, China's latest patents, Technical Efficacy Thesaurus, Application Domain, Technology Topic, Popular Technical Reports.
© 2025 PatSnap. All rights reserved.Legal|Privacy policy|Modern Slavery Act Transparency Statement|Sitemap|About US| Contact US: help@patsnap.com