Mold achieving forming through multi-insert dovetail core-pilling mechanism
A core-pulling mechanism and dovetail technology, applied in the field of product forming molds, can solve problems such as the inability to achieve rapid and precise positioning of silicon steel sheet groups, and achieve the effects of simple and compact structure, stable and reliable work, and improved production efficiency
- Summary
- Abstract
- Description
- Claims
- Application Information
AI Technical Summary
Problems solved by technology
Method used
Image
Examples
Embodiment Construction
[0017] Specific embodiments of the invention will be described in detail below in conjunction with technical text and accompanying drawings.
[0018] When assembling the mold, the fixed mold core 12 is installed in the mold cavity processed by the fixed mold insert 11 and is limited by the hanger, and the fixed mold insert 11 is installed in the mold cavity processed by the fixed mold insert 10 by the hanger. position, the spring A13 is installed in the counterbore hole processed by the fixed template 3, the fixed mold insert 10 is installed in the cavity processed by the fixed template 3, and the bolts pass through the fixed template 3 to lock and fix it with the fixed template 3. The positioning plate 34 is installed in the mold cavity processed by the fixed template 3, and the bolt passes through the fixed template 3 to lock and fix it with the fixed template 3, and the two slider seats 17 are assembled with the slider A16 and the slider B20 respectively, and the bolts Thro...
PUM
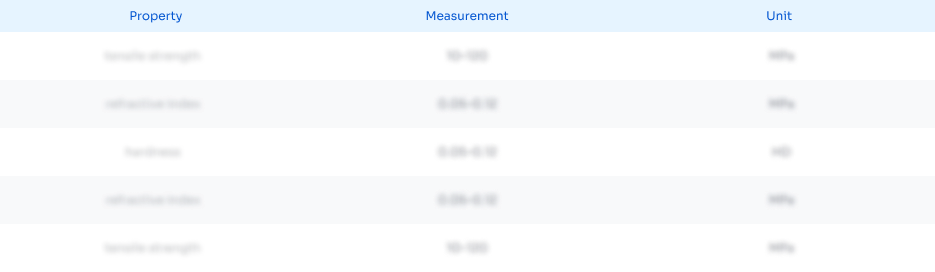
Abstract
Description
Claims
Application Information

- Generate Ideas
- Intellectual Property
- Life Sciences
- Materials
- Tech Scout
- Unparalleled Data Quality
- Higher Quality Content
- 60% Fewer Hallucinations
Browse by: Latest US Patents, China's latest patents, Technical Efficacy Thesaurus, Application Domain, Technology Topic, Popular Technical Reports.
© 2025 PatSnap. All rights reserved.Legal|Privacy policy|Modern Slavery Act Transparency Statement|Sitemap|About US| Contact US: help@patsnap.com