A sensorless brushless DC motor rotor commutation error correction method and control system
A brushed DC motor and error correction technology, applied in the direction of electronic commutation motor control, control system, electrical components, etc., can solve the problems of reducing motor efficiency, increasing motor torque ripple, etc., to improve commutation accuracy, reduce Effect of Error Convergence Time
- Summary
- Abstract
- Description
- Claims
- Application Information
AI Technical Summary
Problems solved by technology
Method used
Image
Examples
Embodiment Construction
[0045] like figure 1 Shown, the method of the present invention realizes as follows:
[0046] In the first step, the system detects the rotor position according to the zero-crossing point of the back EMF of the non-conducting phase, and delays the zero-crossing point of the opposite electric potential by 30 electrical degrees according to the speed measurement information to generate the actual commutation signal.
[0047] In the second step, according to the error calculation method, the controller collects the voltage difference and calculates the commutation error from the error solution equation.
[0048] In the third step, the controller superimposes the appropriate compensation value into the commutation signal according to the commutation error, and then drives the motor to run.
[0049] In the fourth step, the control system repeats the first step to the third step to realize the closed-loop correction of the commutation error and drive the motor to run.
[0050] lik...
PUM
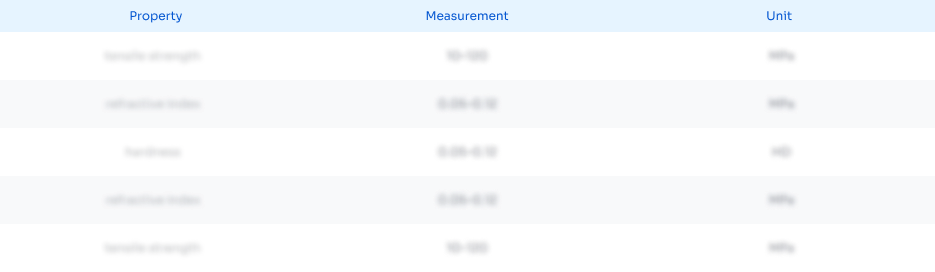
Abstract
Description
Claims
Application Information

- Generate Ideas
- Intellectual Property
- Life Sciences
- Materials
- Tech Scout
- Unparalleled Data Quality
- Higher Quality Content
- 60% Fewer Hallucinations
Browse by: Latest US Patents, China's latest patents, Technical Efficacy Thesaurus, Application Domain, Technology Topic, Popular Technical Reports.
© 2025 PatSnap. All rights reserved.Legal|Privacy policy|Modern Slavery Act Transparency Statement|Sitemap|About US| Contact US: help@patsnap.com