Rotor to undergo coiling and process of performing coiling on rotor
A winding and rotor technology, applied in the field of rotors, can solve the problems of low winding efficiency, easy running out of wires, and high scrap rate, and achieve the effects of convenient winding, firm fixation, and improved work efficiency.
- Summary
- Abstract
- Description
- Claims
- Application Information
AI Technical Summary
Problems solved by technology
Method used
Image
Examples
Embodiment Construction
[0027] The specific implementation manners of the present invention will be further described in detail below in conjunction with the accompanying drawings and embodiments. The following examples are used to illustrate the present invention, but are not intended to limit the scope of the present invention.
[0028] Such as figure 1 and figure 2 The shown rotor to be wound specifically includes a rotating shaft 1 and several layers of stacked rotor pieces 2; The edge is provided with a plurality of connecting pieces 22 uniformly distributed circularly along the rotating shaft 1; one end of each connecting piece 22 is connected with the mounting piece 21, and the other end is provided with a straight side 23 so that all the straight sides 23 form a regular polygon, so A notch 24 is provided between the two adjacent straight sides 23 .
[0029] Specifically, one end of the above-mentioned connecting piece 22 is located at the center of the straight side 23 and is perpendicula...
PUM
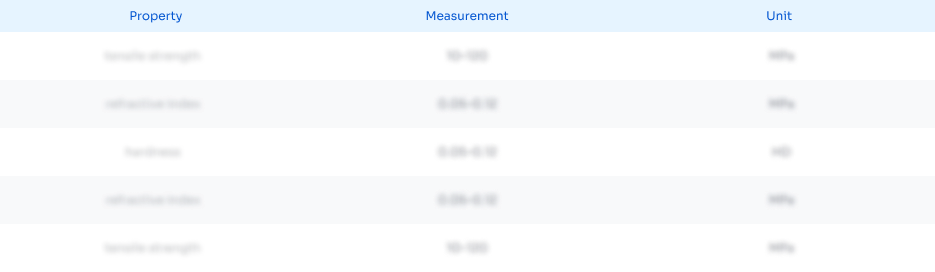
Abstract
Description
Claims
Application Information

- R&D
- Intellectual Property
- Life Sciences
- Materials
- Tech Scout
- Unparalleled Data Quality
- Higher Quality Content
- 60% Fewer Hallucinations
Browse by: Latest US Patents, China's latest patents, Technical Efficacy Thesaurus, Application Domain, Technology Topic, Popular Technical Reports.
© 2025 PatSnap. All rights reserved.Legal|Privacy policy|Modern Slavery Act Transparency Statement|Sitemap|About US| Contact US: help@patsnap.com